Advantages of Using Cnc Metal Cutting in Modern Manufacturing
In the realm of modern manufacturing, the quest for precision and efficiency has led to the widespread adoption of advanced machining technologies. Among these innovations, CNC metal cutting stands out as a transformative process that has redefined how engineers and manufacturers approach metal fabrication. By leveraging the capabilities of Computer Numerical Control (CNC) systems, businesses can achieve unparalleled accuracy, repeatability, and speed in cutting various metals, catering to the increasing demands of today's fast-paced production environments.
The advantages of using CNC metal cutting extend beyond mere operational efficiency; they encompass improved safety, reduced material waste, and the ability to execute complex designs that were once thought unattainable. As industries strive for competitiveness and sustainability, embracing CNC metal cutting technology not only elevates product quality but also enhances overall manufacturing processes. In this blog, we will explore the myriad benefits of CNC metal cutting and why it has become an essential tool in the toolkit of modern manufacturers.
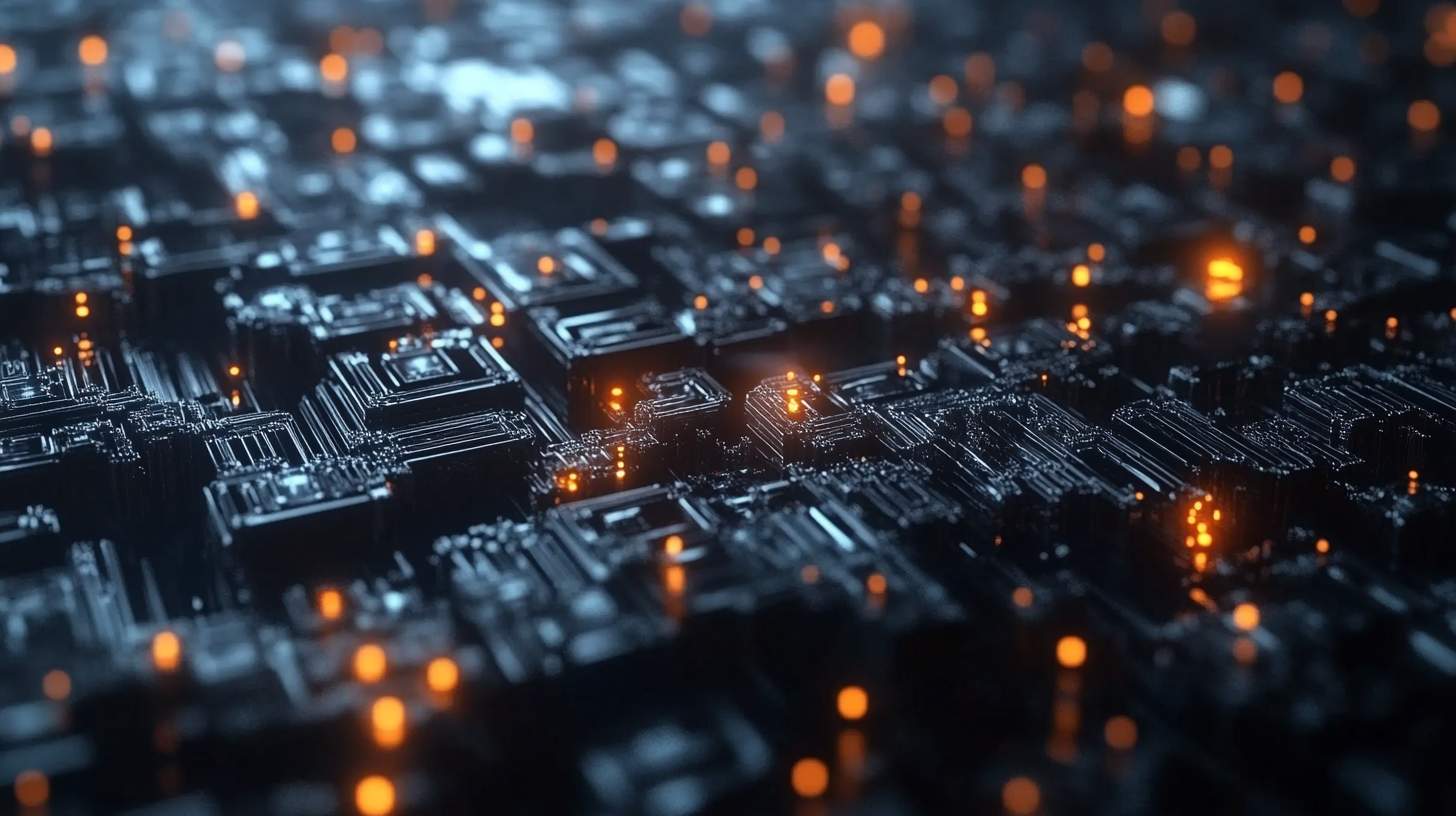
Benefits of CNC Metal Cutting for Precision Engineering
CNC metal cutting has revolutionized precision engineering, offering numerous benefits that are increasingly important in modern manufacturing. One of the most significant advantages is the high level of precision it provides. CNC machines can operate with tolerances as tight as fractions of a millimeter, ensuring that components meet the stringent requirements of advanced engineering applications. This precision is critical for industries like aerospace and automotive, where even the smallest deviation can lead to costly failures. Another benefit of CNC metal cutting is its efficiency in producing complex shapes. Traditional machining methods can struggle with intricate designs, leading to longer production times and increased material waste. Conversely, CNC technology allows for the easy programming of complex geometries, significantly reducing production times and optimizing material usage. This not only enhances productivity but also contributes to lower production costs, providing a competitive edge in a market that demands both quality and affordability. Furthermore, the adaptability of CNC metal cutting systems is noteworthy. As production needs change, these machines can be quickly reprogrammed to accommodate new designs or specifications without the need for extensive retooling. This flexibility enables manufacturers to respond rapidly to market demands, supporting innovation and customization in their product offerings. As industries continue to evolve towards more specialized and tailored solutions, the role of CNC metal cutting in precision engineering only becomes more central.
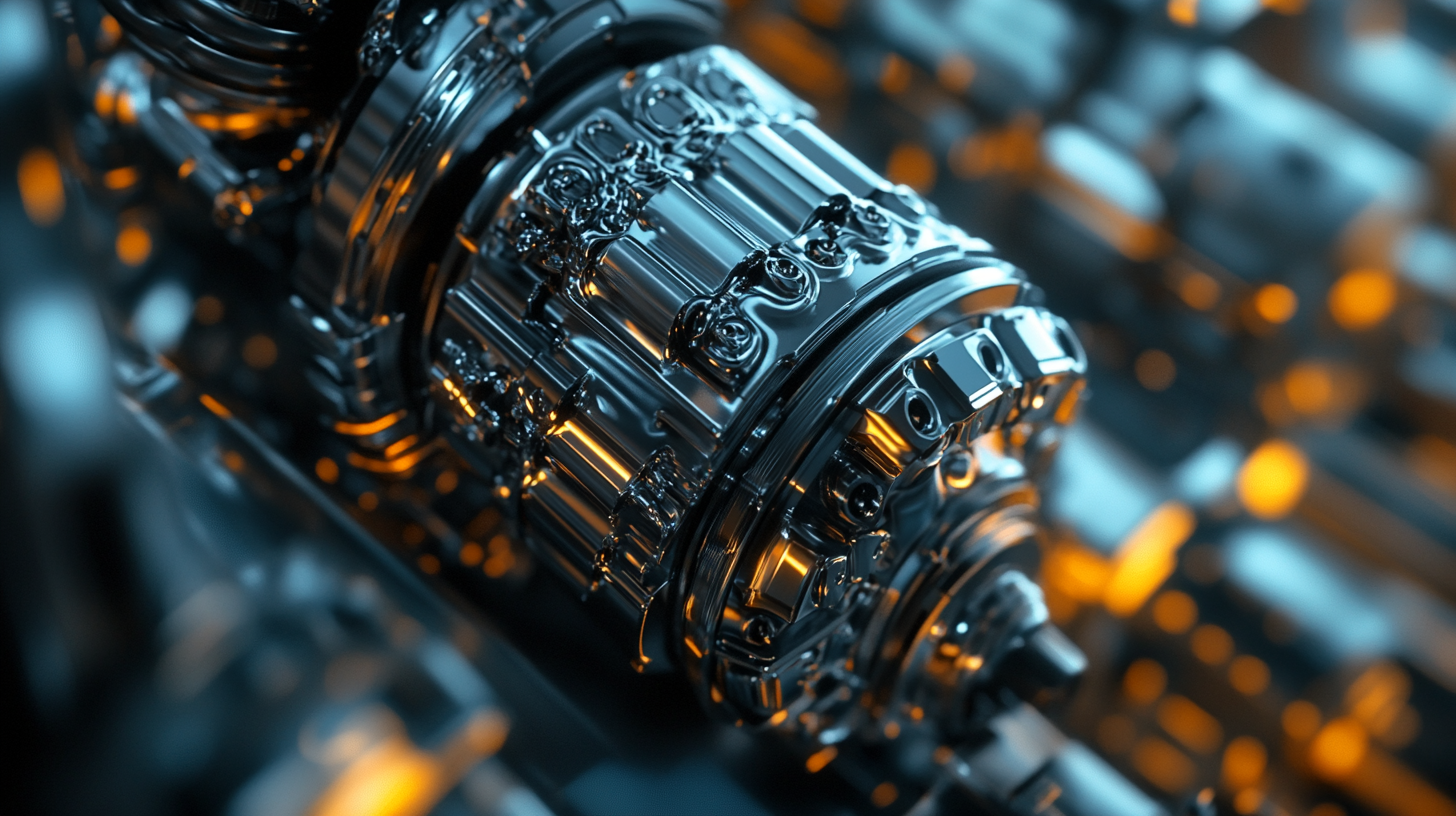
Enhanced Efficiency and Speed in Production Processes
The rise of CNC (Computer Numerical Control) metal cutting technology has revolutionized modern manufacturing, particularly in enhancing efficiency and speed in production processes. According to a report by Mordor Intelligence, the global CNC machine market is expected to grow at a compound annual growth rate (CAGR) of 5.6% from 2021 to 2026. This growth underscores the increasing reliance on CNC machining to streamline operations, minimize waste, and improve product quality.
CNC metal cutting offers remarkable precision, which significantly reduces the runtime for machining processes. A study by PwC found that companies using CNC technology can cut their production time by up to 50% compared to traditional methods. This is especially critical in industries such as aerospace and automotive, where tight tolerances and high production demands necessitate advanced manufacturing capabilities. CNC machines can operate continuously without sacrificing quality, allowing manufacturers to meet tight deadlines and increase throughput.
Furthermore, the automation provided by CNC technology ensures consistency in production. The National Institute of Standards and Technology (NIST) reports that the integration of CNC systems can lead to a reduction in human errors by over 90%. Automated programming and machining ensure that every piece produced adheres to exact specifications, thus enhancing overall production reliability. As manufacturers continue to adopt CNC metal cutting, they not only achieve greater speed and efficiency but also enhance their competitiveness in an increasingly demanding market landscape.
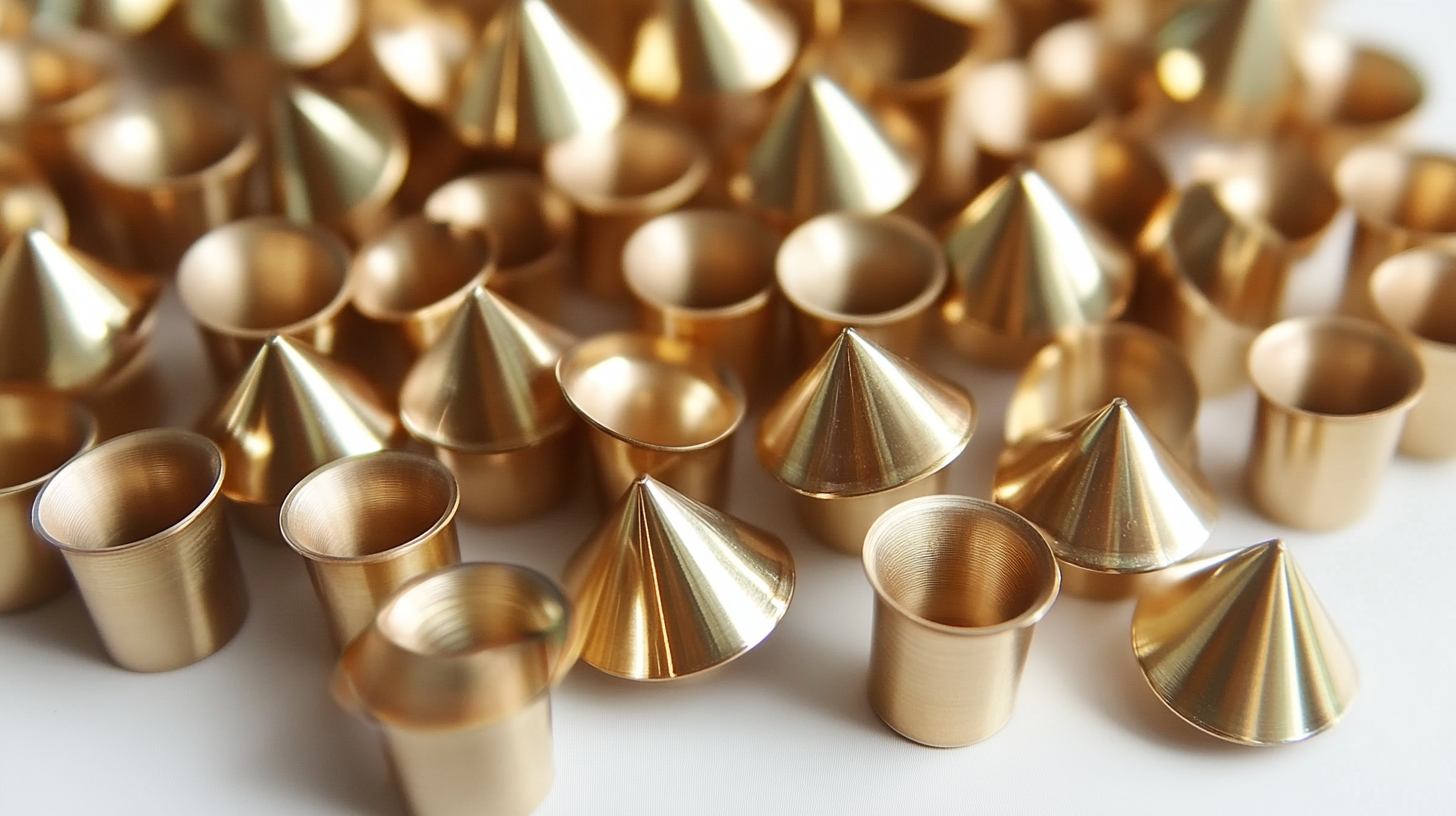
Cost-Effectiveness: Reducing Waste and Labor Costs
The adoption of CNC metal cutting technology in modern manufacturing plays a pivotal role in enhancing cost-effectiveness, primarily by minimizing waste and reducing labor costs. As industries strive for greater efficiency, the introduction of CNC (Computer Numerical Control) machines allows manufacturers to achieve precise cuts with minimal material waste, aligning with global standards in sustainability and resource management.
Recent statistics illustrate the profound impact that waste reduction can have on overall operational costs. For instance, businesses across various sectors are grappling with the financial burden caused by waste, with food waste accounting for a staggering 1.3 billion tons annually worldwide. This emphasizes the necessity for effective waste management strategies, which CNC machining synergistically supports by ensuring that materials are utilized to their fullest potential. By significantly lowering scrap rates, companies not only enhance their profitability but also mitigate the environmental impacts associated with excessive waste.
Furthermore, employing CNC technology reduces labor costs through automation and precision. Unlike traditional manufacturing methods, CNC machines require less manual intervention, which translates to lower labor expenses and a decrease in human error. In a landscape marked by rising inflation and supply chain challenges, this efficiency becomes crucial for manufacturers looking to control costs and maintain competitiveness. As the manufacturing sector continues to evolve, the integration of CNC metal cutting technology stands out as an optimal solution for businesses aiming to enhance productivity while promoting sustainable practices.
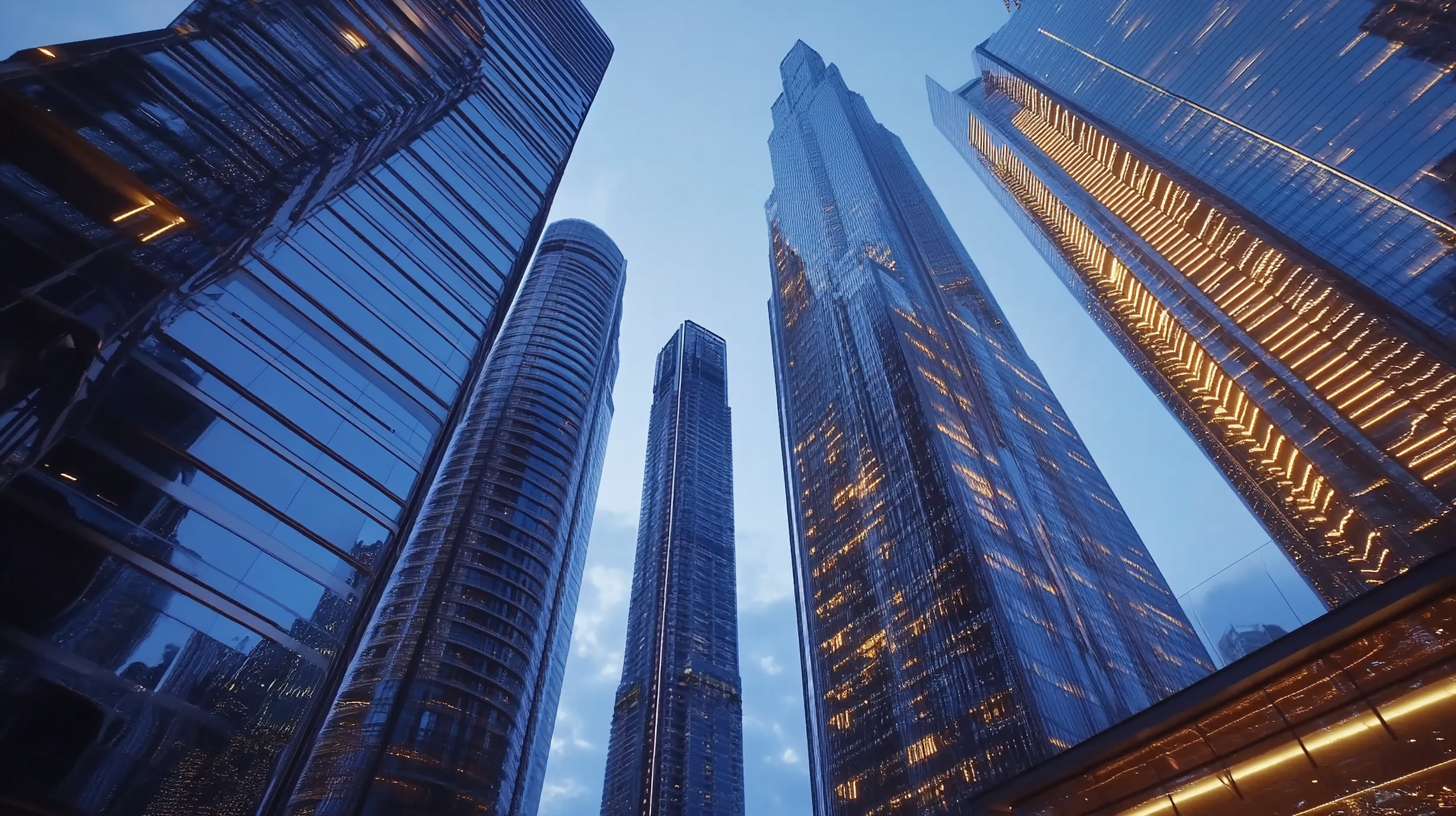
Flexibility and Versatility in Material Handling
In the realm of modern manufacturing, the flexibility and versatility of CNC metal cutting have emerged as game-changers. According to a report by Market Research Future, the global CNC machine market is projected to reach $100 billion by 2025, highlighting the increasing reliance on CNC technologies across various industries. One of the key advantages of CNC metal cutting is its ability to handle a diverse range of materials, from aluminum and steel to harder alloys and composites. This adaptability allows manufacturers to tailor their production processes to meet specific project requirements, enhancing efficiency and output.
Moreover, the precision offered by CNC machines means that manufacturers can achieve tighter tolerances and intricate designs that would be challenging or impossible with traditional cutting methods. Research from the National Institute of Standards and Technology indicates that CNC technology can improve production speed by up to 30%, reducing lead times and increasing the capability to respond swiftly to market demands. This rapid adaptability not only helps manufacturers optimize their processes but also enables them to explore new market opportunities without the constraints of fixed tooling setups.
Further emphasizing this versatility, manufacturers can switch from cutting one material type to another with minimal downtime. This is particularly beneficial in industries such as aerospace and automotive, where diverse materials are frequently used in the same production line. A report from the American Society for Precision Engineering suggests that the ability to seamlessly transition between materials can lead to a 20% reduction in material waste, thereby not only enhancing operational efficiency but also promoting sustainability within manufacturing processes.
Improving Safety Standards in Manufacturing Environments
In modern manufacturing, the integration of CNC (Computer Numerical Control) metal cutting technology significantly enhances safety standards within production environments. Traditional machining methods often involve manual operations, which can lead to various hazards, including accidents caused by human error. However, CNC machines are designed to operate autonomously with minimal human intervention, reducing the risk of personal injury.
Moreover, CNC metal cutting machines are equipped with advanced safety features that protect operators and nearby workers. These include automatic shutdown mechanisms, emergency stop buttons, and protective enclosures that limit exposure to hazardous processes. The precision of CNC machines also minimizes the likelihood of mistakes that could result in dangerous situations, such as tool breakage or errant cuts.
Additionally, implementing CNC cutting technology streamlines workflow, allowing for better organization of the workspace. This organized environment reduces clutter, which is often a significant factor in workplace accidents. By using CNC technology, manufacturers can not only produce high-quality parts with improved accuracy but also create a safer atmosphere that prioritizes the well-being of their workforce. This dual benefit makes CNC metal cutting an essential aspect of modern manufacturing practices.