Maximizing Efficiency and Reducing Downtime with Cnc Plasma Cutter Maintenance Tips
The CNC plasma cutter is an important piece of equipment capable of delivering productivity and accuracy in the generally competitive field of metal fabrication. In its report on the said sector, IBISWorld mentions that the sustained growth of metal cutting services occurs at a rate of around 2.1% per year, due primarily to advances in cutting technologies. It is during this phase that productivity of the machines becomes even more vital for the competitiveness of the companies employing these machines. A preventive maintenance system does not just ensure a longer life of the machine; it also minimizes downtime, which can become very costly and interrupt a production schedule.
Industry sources indicate that unplanned downtime can account for almost 10% of total productivity in the manufacturing shop, emphasizing the need to develop maintenance strategies. Assurance for better performance of a CNC plasma cutter indicates fewer breakdowns and continuity of high-quality output through good maintenance tips. This blog will cover some maintenance tips for maintaining the highest operational efficiency while ensuring longevity for CNC plasma cutting machines. This information would prove invaluable for anyone in the metalworking and fabrication industry.
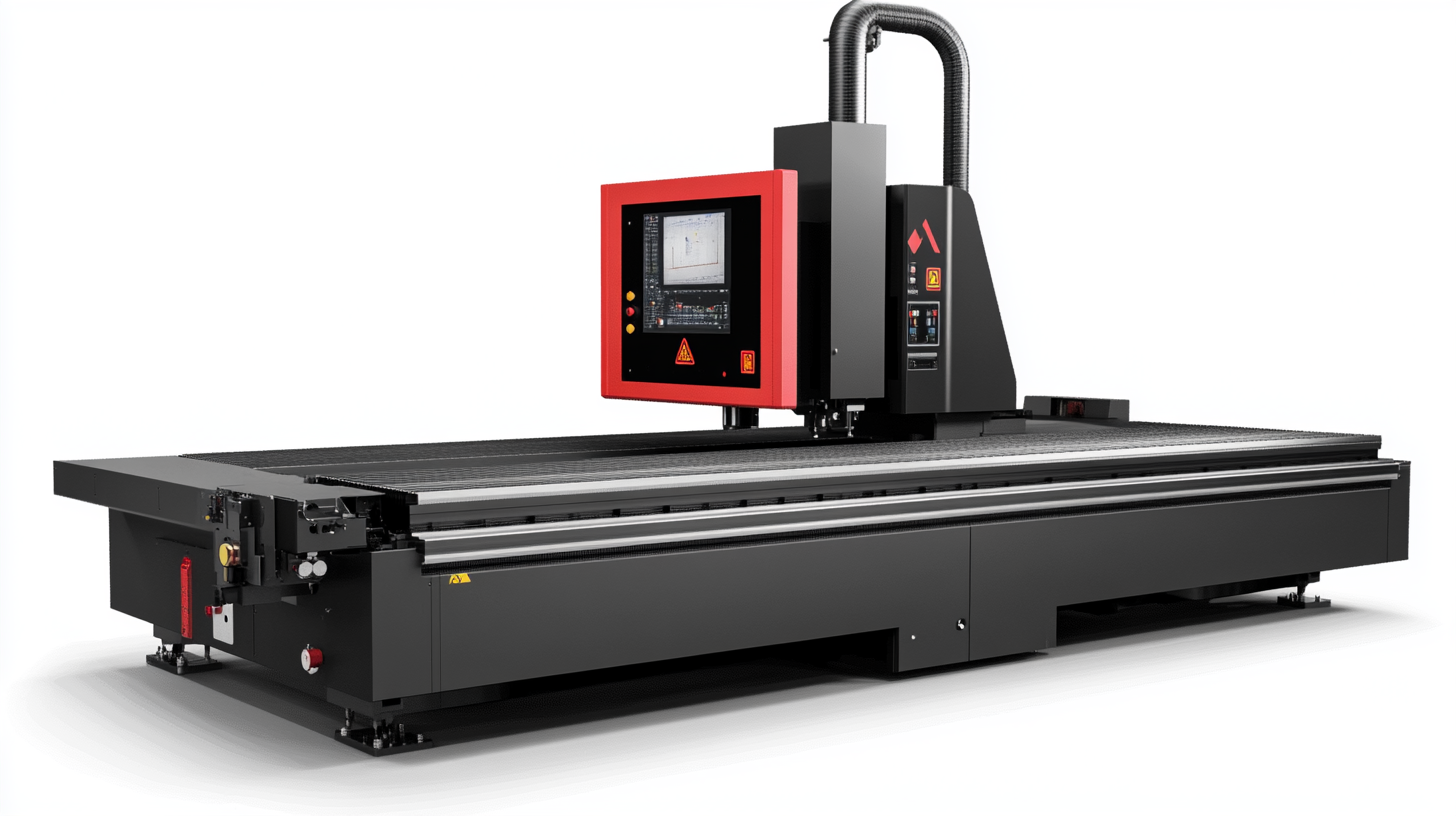
Best Practices for Daily CNC Plasma Cutter Maintenance
Daily maintenance is very essential for CNC plasma cutters to maximize their efficiency and minimize downtime. According to a report published by the Fabricators & Manufacturers Association, nearly 30% of machine downtime is caused by problems that pertain to maintenance. Following best practices for daily upkeep can really add life to these machines and ensure all-time high-quality production. One practice would be a daily check of the cutting head and consumables. Regular checking of nozzles and electrodes for any wearing out will save a lot of money in repair and loss of precision. The American Welding Society states that replacing worn-out consumables may increase the quality of cuts and reduce machine failure rates by as much as 25%. Also, keeping air and water filters clean will help enhance performance and avoid unnecessary downtimes through operation inconsistencies. Another critical aspect of daily maintenance includes calibration of the CNC system. Correct calibration of the machine not only improves the accuracy of the cutting but also the efficiency of the entire operation. Reports show that machines that have calibration conducted habitually have displayed productivity rates that are equal to above 15% as compared to those that haven't. Further, keeping comprehensive records on maintenance assists in following performance and determining trends that possibly could indicate issues deeper down the line and help avoid unexpected breakdowns. So with the following daily maintenance, all operators will ensure their CNC plasma cutters cast longer, even as they optimize production.
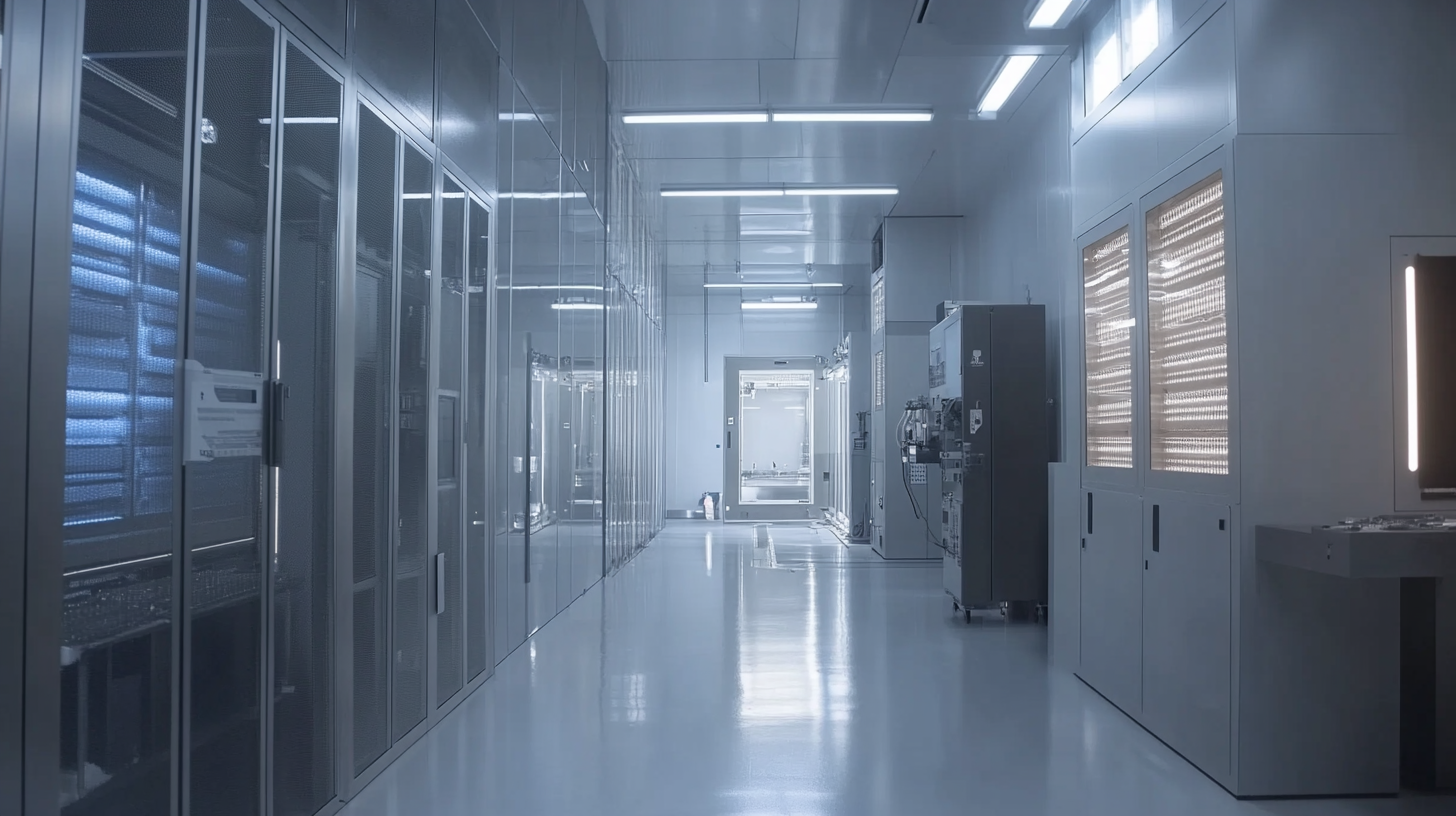
Identifying Common Issues to Prevent Downtime
To maximize efficiency and reduce downtime with CNC plasma cutters, regular maintenance is very important. Operators can smooth out their operations and prevent interruptions by identifying common issues before they turn into real problems. Among the most common issues are poor torch performance, because of either consumables that have been used too long or wrong gas flow; the regular inspection and replacement of these parts will greatly increase the cut quality and consistency while reducing the likelihood of unexpected failure of the equipment.
Electrical problems are another frequent occurrence and can be triggered mainly by either loose connections or damaged components. Tightening all connections and ensuring that wire insulation is intact could prevent any situation causing a short circuit that could put equipment down. Also, monitoring the computer and software system that controls the CNC cutter is essential; updating the software and regular checks of the systems may avoid glitches that interfere with production.
Finally, cleaning and maintaining the machinery will avoid future problems. Dust and metal shavings can accumulate over time and give rise to overheating and mechanical failure. Therefore, by establishing a healthy cleaning routine and carrying out good supervision as well as maintenance, the equipment will always be in good condition and thus be less likely to suffer downtime. When operators do these things on a proactive basis, they will keep CNC plasma cutters working better and keep them working.
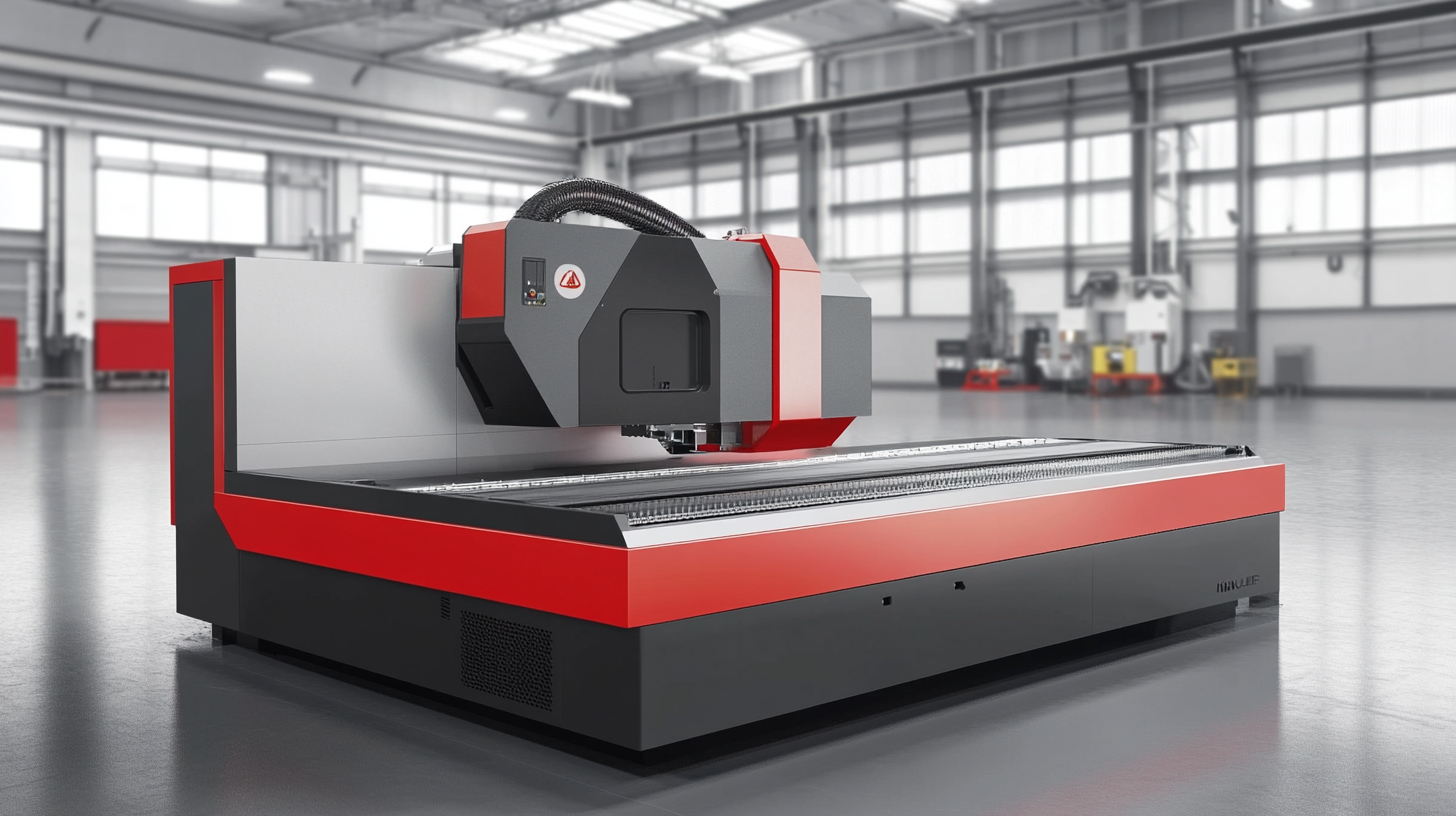
Essential Tools for Effective CNC Plasma Cutter Care
Proper maintenance on CNC plasma cutter facilitates optimal performance of the machine besides increasing its lifespan. One proper care is holding having the right tools; besides, having such tools will not only make routine maintenance easy but will also help in taking care of minor problems before they develop into major problems.
First and foremost, quality gauntlet gloves are essential for safety when doing maintenance. They also protect from sparks and sharp edges while working on the machine; thus giving the user safety when handling their plasma cutter. This includes skin gloves and a strong cleaning kit, with brushes, wipes, and appropriate cleaning agents to keep machine parts free from debris and slag, which can otherwise get in the way of precision cutting or even accelerating wear.
A multimeter comes in handy while troubleshooting electrical issues; measuring levels of voltage and current helps to identify the problem, be it a faulty connections or malfunctioning sensors. A preventative measure for unforeseen downtime, it provides a routine check-up using a multimeter on your CNC plasma cutter. Last but definitely not least, spare consumables like nozzles and electrodes can really save time from production halts and quickly repair equipment, so these are must-haves for any serious plasma cutter maintenance. A well-stocked tool kit ensures optimal efficiency as well in allowing that seamless cutting process that allows your operations to run smoothly.
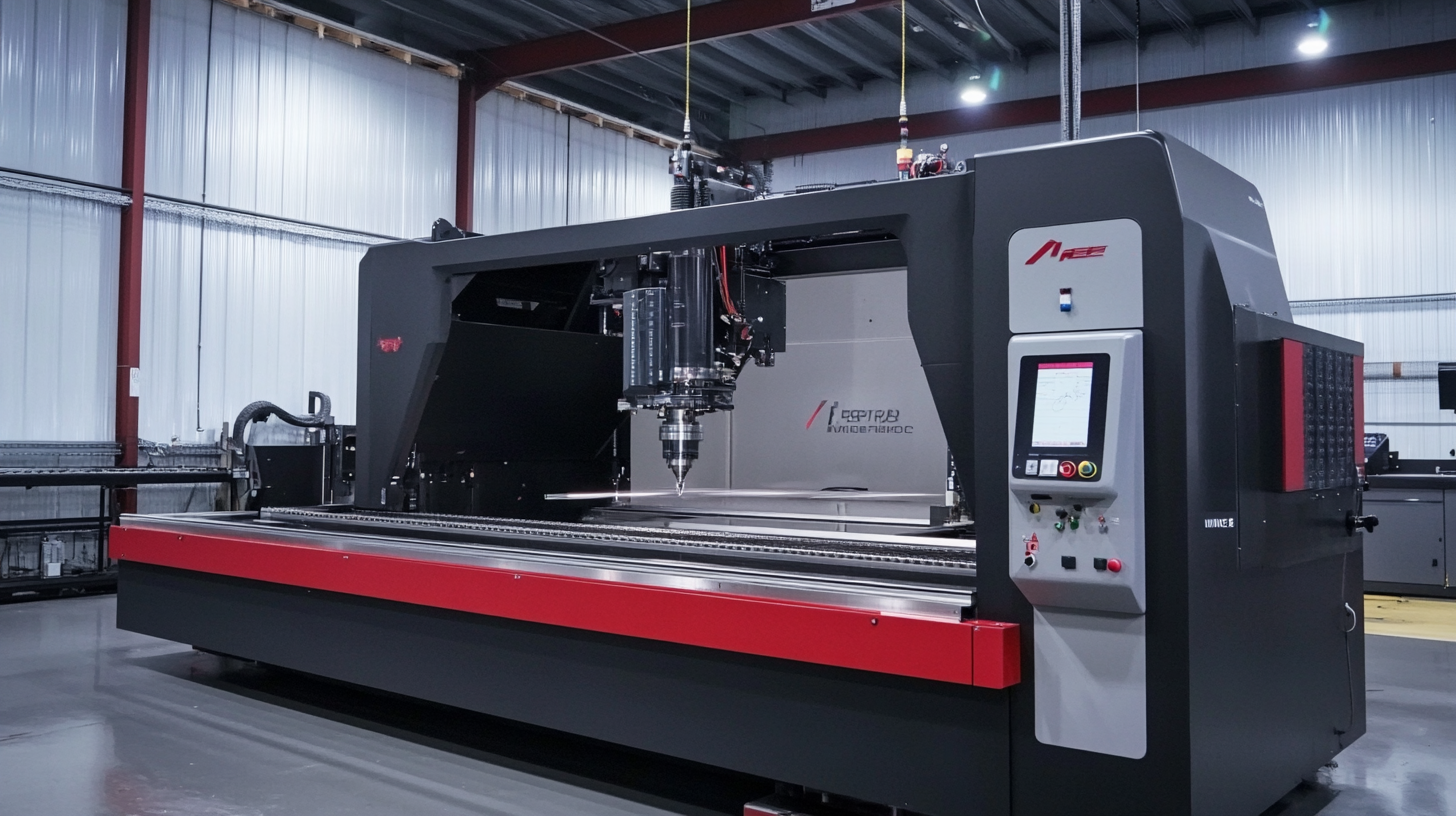
Scheduling Regular Maintenance: A Key to Longevity
Regular maintenance of CNC plasma cutters is extremely useful for their long life and performance. Maintenance checks are very much routine, but scheduling them is a wise, proactive way to save users a lot of time and money in the future. Dedicating certain time intervals for the assessment and maintenance of the equipment will let the operators notice any impending problems before they can be deemed costly repairs or unplanned downtime.
Routine maintenance activities include checking main components, such as the torch, nozzles, and filters, cleaning out the internal systems for any potential buildup, and calibrating the machine for maximum efficiency. The benefits of having a maintenance schedule extend to a smooth performance by the machinery and a safer environment by limiting accidents from malfunctioning machines.
Further, maintenance logs can be used to track wear and tear patterns, enabling operators to make wise choices about upgrades and replacements in the future. A well-maintained CNC plasma cutter provides cleaner cuts, better precision, and ultimately more productivity, so regular maintenance is indeed a crucial aspect of any industrial setting.
Tips for Optimizing Cutting Performance and Accuracy
To keep it cutting clean and accurate with CNC plasma cutters, constant maintenance is required. Well-maintained machines are not only operationally productive but also help prolong the lifespan of equipment and machinery. The cutting performance is kept at its optimum by routine inspection and changing of consumable components like nozzles and electrodes. As these parts get aged with time, they tend to affect the quality of the cuts made by the machines. Therefore, it is always good to monitor their conditions and change them at the first indication of wear or damage.
Keeping the table and cutting surface free from dirt and debris is equally an important tip for cutting accuracy. Contaminants will interfere with the process of value cutting and cause a number of inaccuracies. Periodic cleaning and an organized workspace benefit the operation. Machine settings speed, height, and power are most effective when calibrated according to each material being processed. This helped increase the effectiveness of the plasma cutter by referring some specific parameters, which helps deliver the perfect end-delivering job.
Last but not least, operators have to put some additional emphasis on this section of training. Knowledge is talent that helps them fully understand what the machine can do and how it is set up-in-the-moment decision on cutting can be completely error-free. The better-trained operators are in the best practices of operations and troubleshooting, the more it will optimize everything-done with the quality of output and time it takes to spend on these projects. These advices will not only maximize the cutting performance of CNC plasma operations, but its overall productivity as well.