Exploring Cnc Plasma Options: Maximizing Efficiency and Cost-Effectiveness in Global Sourcing
In today's rapidly evolving manufacturing landscape, businesses are increasingly seeking innovative solutions to enhance productivity while managing costs effectively. One such solution that has gained significant traction is CNC plasma cutting technology. With its precision and efficiency, CNC plasma offers a dynamic option for enterprises looking to optimize their sourcing strategies on a global scale. This blog will delve into the various options available within CNC plasma systems, highlighting their potential to maximize operational efficacy while also reducing financial outlays.
As companies navigate the complexities of global sourcing, understanding the benefits and capabilities of CNC plasma can unlock new opportunities for streamlined production and competitive advantage. By examining the latest advancements in CNC plasma technology, along with practical insights into implementation and supplier selection, we aim to provide a comprehensive guide that empowers businesses to make informed decisions. Ultimately, leveraging CNC plasma effectively can not only accelerate production timelines but also lead to significant cost savings, making it an essential consideration for manufacturers in today's market.
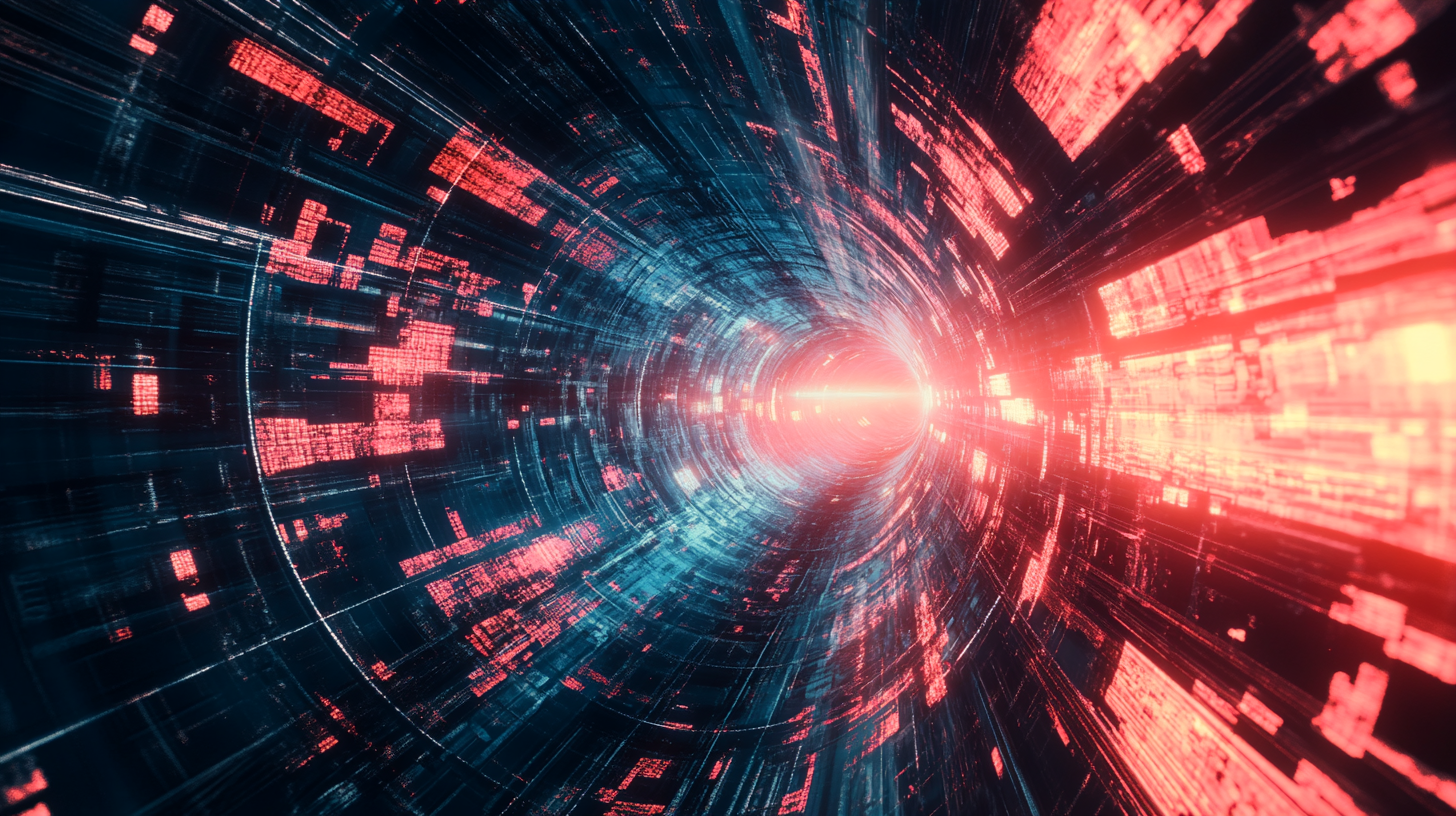
Understanding CNC Plasma Cutting: Basics and Advantages
CNC plasma cutting is a transformative technology in the manufacturing industry, representing a blend of precision and versatility. Understanding the basics of CNC plasma cutting reveals its fundamental advantages over traditional cutting methods. CNC, or Computer Numerical Control, allows for automated and highly accurate cutting of various materials, enhancing productivity. With capability to cut intricate designs in metal sheets, it has become a go-to method for industries that require both efficiency and quality. The advantages of CNC plasma cutting extend beyond just speed and precision. The technology allows for the efficient use of materials, minimizing waste and reducing overall costs in production. Recent advancements in plasma cutting have introduced data-rich features that help in managing consumables effectively, contributing to cost savings in operational setups. Additionally, the ability to work with thick metals means that CNC plasma cutting is invaluable in sectors like construction and manufacturing, where robust materials are a necessity. As industries embrace global sourcing, the efficiency and cost-effectiveness of CNC plasma cutting positions it as a critical tool in modern manufacturing strategies. Moreover, hands-on exposure to these technologies is increasingly important, as highlighted by initiatives to encourage young women into skilled trades. Such initiatives aim to equip the next generation with the necessary skills in areas like welding and CNC machining, fostering a strong workforce familiar with cutting-edge techniques. This emphasis on skills development is integral as industries seek to optimize their operations through advanced technologies like CNC plasma cutting.
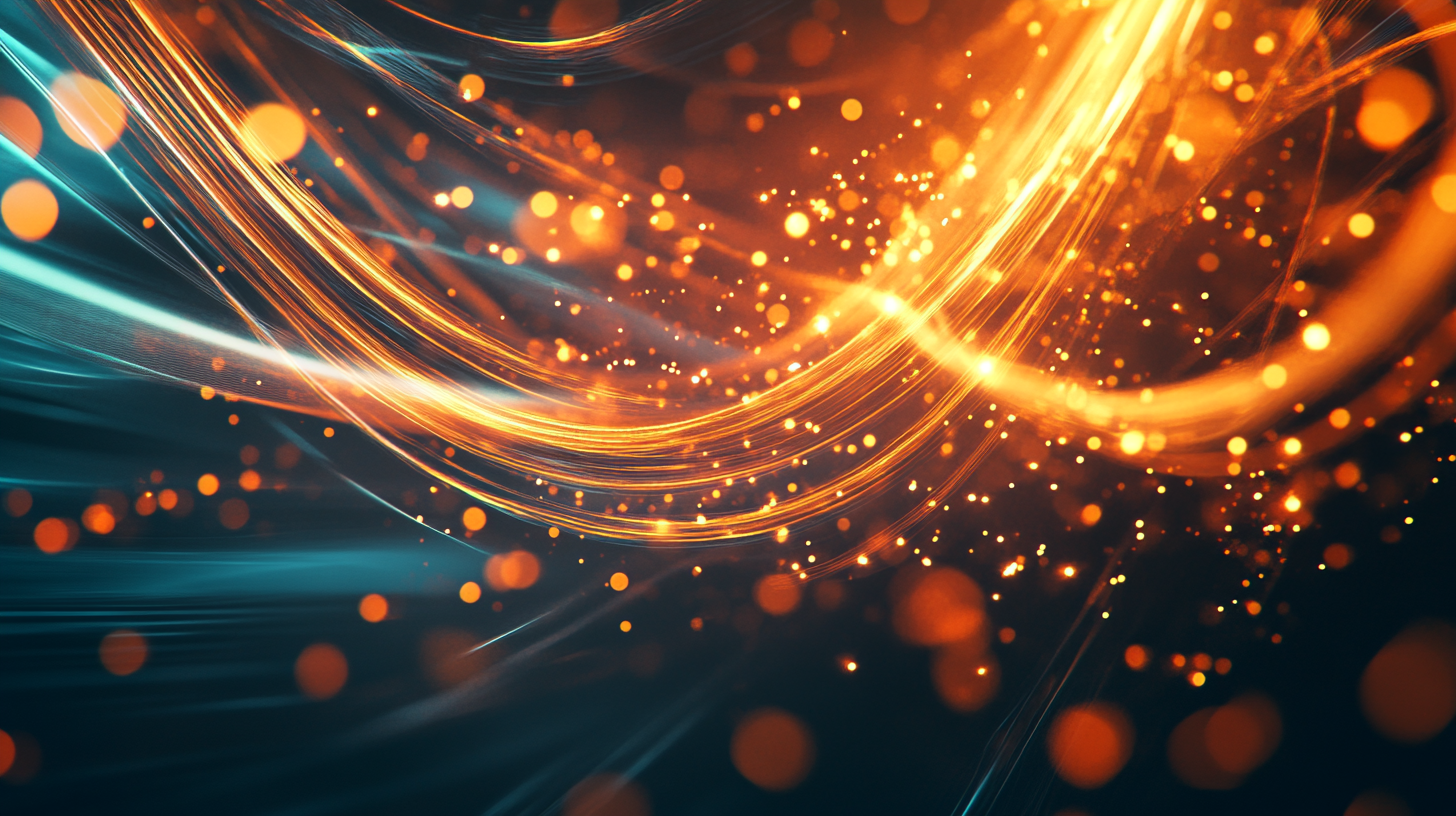
Key Factors Influencing Efficiency in CNC Plasma Operations
CNC plasma cutting technology plays a crucial role in various industrial applications, where efficiency and cost-effectiveness are paramount. The market for CNC plasma cutting machines is experiencing significant growth, projected to reach USD 722 million by 2032. This expansion emphasizes the increasing reliance on CNC technology to streamline operations and reduce production costs. As businesses explore global sourcing options, understanding the key factors that influence efficiency in CNC plasma operations becomes essential.
One of the primary factors affecting efficiency is the quality of the plasma cutting machine itself. High-performance CNC machines, equipped with advanced features such as precision control and automated settings, can dramatically enhance cutting speed and accuracy. Additionally, maintenance practices and regular calibration of these machines are crucial for maintaining peak performance. Operators must also be trained in optimizing machine settings to suit specific materials and thicknesses, ensuring that the cutting process is both efficient and economical.
Another important aspect is the material selection, as different materials respond uniquely to plasma cutting. Factors such as thickness, type of metal, and surface condition can significantly impact cutting efficiency. Furthermore, employing the right cutting parameters for each material can minimize waste and reduce operational costs. As manufacturers increasingly prioritize efficiency, investing in quality CNC plasma cutting machinery and proper training for operators is essential for organizations aiming to thrive in the competitive landscape of global sourcing.
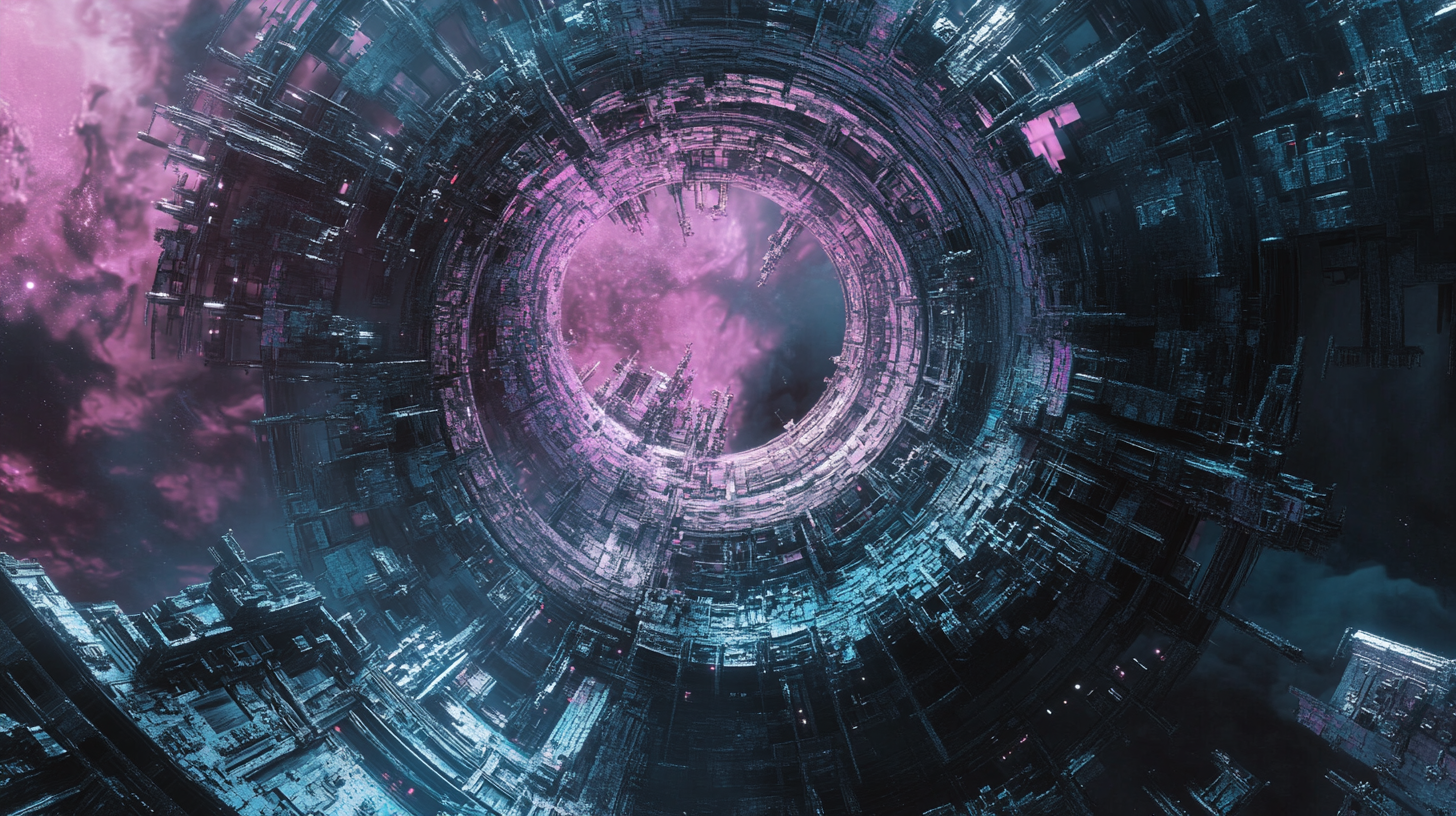
Cost-Effective Strategies for Global Sourcing of CNC Plasma Equipment
The global plasma cutting machine market is poised for significant growth, expected to expand from $646.2 million in 2023 to $841.4 million by 2030. As industries seek efficiency and cost-effectiveness, CNC plasma equipment becomes a pivotal choice for manufacturers looking to streamline operations and reduce overhead costs. This growth reflects not only rising demand but also the increasing sophistication of technology emanating from innovators in regions like China.
China is rapidly establishing itself as a leader in the advanced manufacturing sector, characterized by enhanced innovation capabilities. The country's universities and domestic companies are at the forefront of developing cutting-edge CNC plasma solutions that cater to diverse industrial needs. For organizations looking to optimize their sourcing strategies, partnering with Chinese manufacturers offers access to state-of-the-art equipment at competitive prices, thereby maximizing cost-effectiveness without compromising on quality.
To harness these advantages, companies need to adopt proactive global sourcing strategies that prioritize building relationships with key players in the Chinese market. By leveraging the latest technological advancements and collaborative innovation, businesses can secure high-performance CNC plasma solutions that drive productivity and profitability. This approach not only fosters financial savings but also positions companies to thrive amid growing global competition.
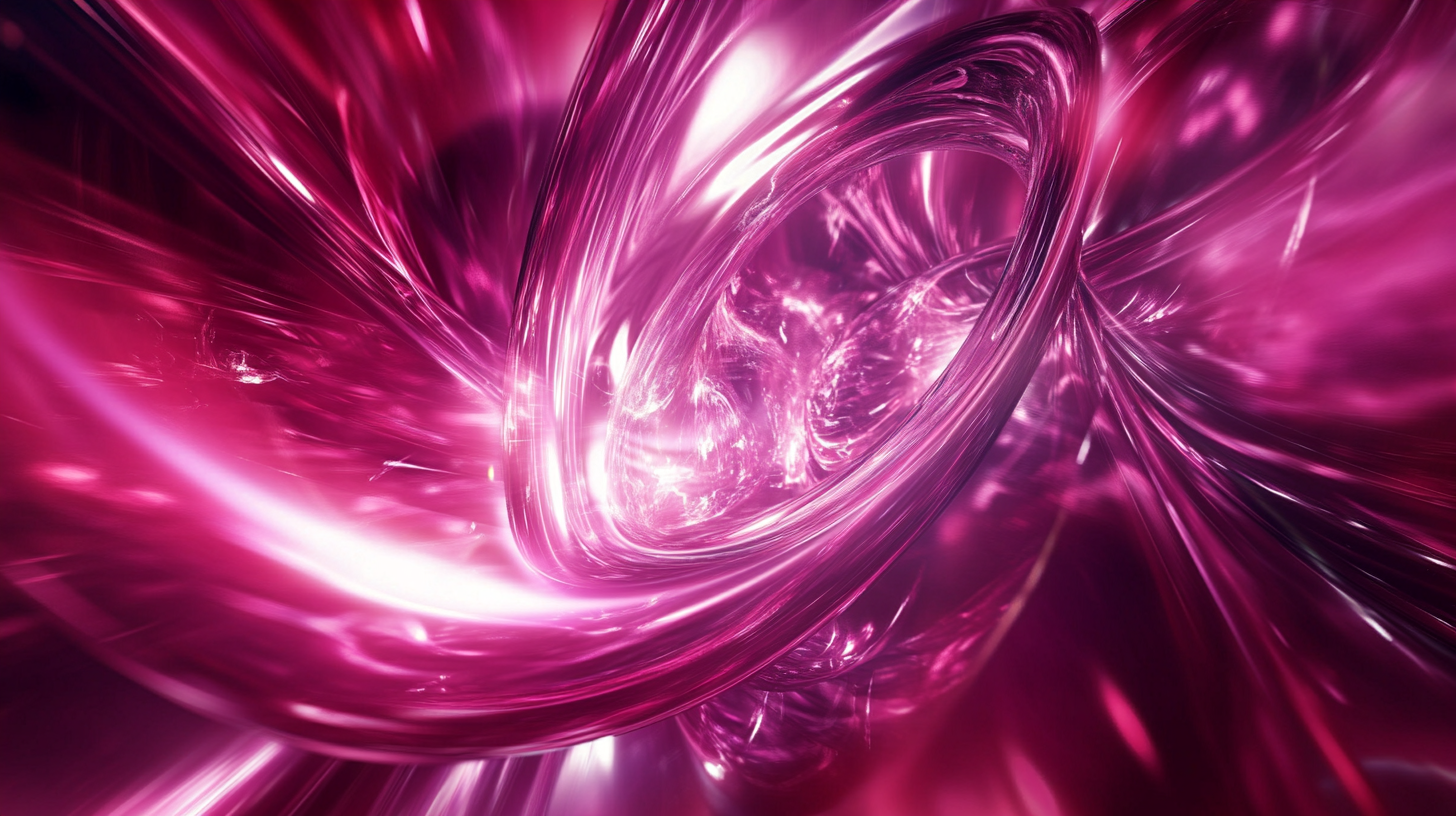
Common Challenges in CNC Plasma and How to Overcome Them
When exploring CNC plasma cutting options, users often face common challenges that can hinder efficiency and cost-effectiveness. One frequent issue is the initial setup and calibration of the CNC plasma system. This stage is crucial, as improper calibration can lead to inaccurate cuts and wasted materials. To overcome this, it is essential to invest time in comprehensive setup procedures and utilize advanced software that aids in precision adjustments. Regular training for operators can also ensure that they understand the nuances of machinery and their impact on the output quality.
Another significant challenge is the consistency of the plasma cutting consumables. Variations in quality among electrodes and nozzles can adversely affect performance, leading to higher operational costs and reduced productivity. To tackle this, it's advisable to establish strong relationships with reliable suppliers who specialize in high-quality materials. Implementing a routine maintenance schedule for the equipment can also mitigate issues related to wear and tear, ensuring that the system operates at peak performance.
Additionally, integrating advanced technologies such as automated nesting software can significantly enhance productivity. This software optimizes material usage by arranging cutting patterns efficiently, minimizing waste. By addressing these challenges with proactive strategies, CNC plasma users can maximize their operational efficiency while also controlling costs in a competitive global sourcing environment.
Future Trends in CNC Plasma Technology for Enhanced Performance
The landscape of CNC plasma technology is rapidly evolving, driven by advancements in automation and digital integration. As industries seek enhanced performance, the next wave of CNC plasma systems is emphasizing precision, efficiency, and user-friendliness. Future trends indicate a shift towards smart technologies that incorporate AI and machine learning, enabling systems to optimize cutting paths in real-time and reduce waste. This cutting-edge approach not only enhances performance but also contributes significantly to sustainability initiatives by minimizing energy consumption and raw material use.
Another notable trend is the increasing integration of IoT capabilities within CNC plasma machines. By allowing for seamless connectivity and data exchange, manufacturers can monitor performance metrics remotely, leading to proactive maintenance and reduced downtime. This connectivity supports a more responsive production environment where adjustments can be made swiftly based on real-time data, ultimately enhancing overall operational efficiency. Furthermore, cloud-based platforms are set to revolutionize how companies manage design and production workflows, facilitating collaboration and accelerating project timelines.
As these technologies evolve, the industry is likely to witness a surge in modular designs, enabling manufacturers to customize their CNC plasma systems based on specific needs and applications. This flexibility is essential for adapting to diverse manufacturing demands, ensuring that businesses can scale operations without incurring excessive costs. By staying abreast of these emerging trends, companies can not only maximize their efficiency but also achieve cost-effectiveness in their global sourcing strategies, positioning themselves competitively in the marketplace.