Exploring the Versatile Features of CNC Plasma Tables and How to Choose the Right One for Your Needs
In recent years, the demand for CNC plasma tables has surged, reflecting a growing recognition of their versatility and efficiency in various manufacturing sectors. According to a report by Research and Markets, the CNC plasma cutting machine market is expected to grow at a CAGR of 5.4% from 2021 to 2026, driven by advancements in technology and the increasing need for high-precision cutting solutions. As industries look for ways to enhance productivity while maintaining cost-effectiveness, the CNC plasma table has emerged as a pivotal tool that combines speed, accuracy, and flexibility.
However, with a plethora of options available on the market, choosing the right CNC plasma table can be a daunting task. Factors such as table size, cutting thickness, and software compatibility require careful consideration to ensure optimal performance and alignment with specific business needs. According to a study by MarketsandMarkets, the integration of automation and smart technology in CNC plasma tables is also reshaping the landscape, offering unprecedented control and efficiency to end-users. This blog aims to explore the versatile features of CNC plasma tables and provide guidance on how to select the ideal model tailored to your operational requirements.
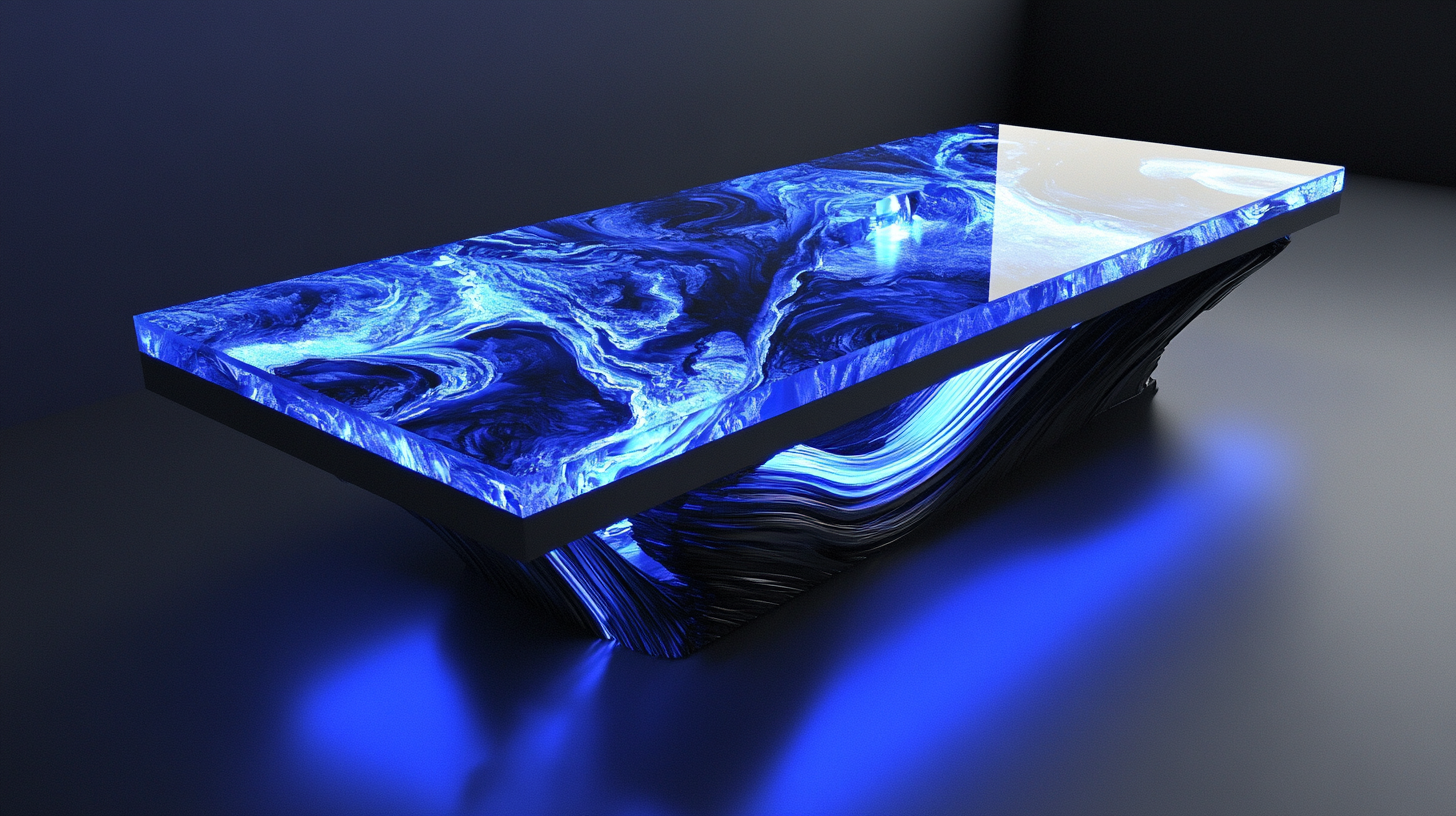
Understanding CNC Plasma Tables: Key Components and Functionality
CNC plasma tables have become essential tools for metal fabricators, hobbyists, and DIY enthusiasts alike. Understanding the key components and functionalities of these machines is crucial when choosing the right one for your specific needs. At the core of a CNC plasma table is its cutting system, which utilizes a high-velocity jet of ionized gas to cut through conductive materials. The precision of the cutting process is largely influenced by the machine's components, including its drive system, control software, and the quality of the plasma torch. When selecting a CNC plasma table, consider factors such as the size of the work area, cutting speed, and the thickness of materials it can handle. For instance, advancements in the market have led to machines capable of cutting larger sheets, with some tables extending up to 10 feet wide and 24 feet long. Additionally, specific features such as adjustable cutting tables and integrated troubleshooting systems enhance usability and efficiency, catering to various project demands. Emerging innovations like specialized fluids capable of preventing rust and corrosion further expand the functionality of CNC plasma tables. As the industry continues to evolve, DIY projects are also gaining traction, with options to build affordable CNC plasma cutters available for those who enjoy hands-on fabrication. This versatility in functionality and the breadth of available models make CNC plasma tables a vital asset for anyone involved in metalworking.
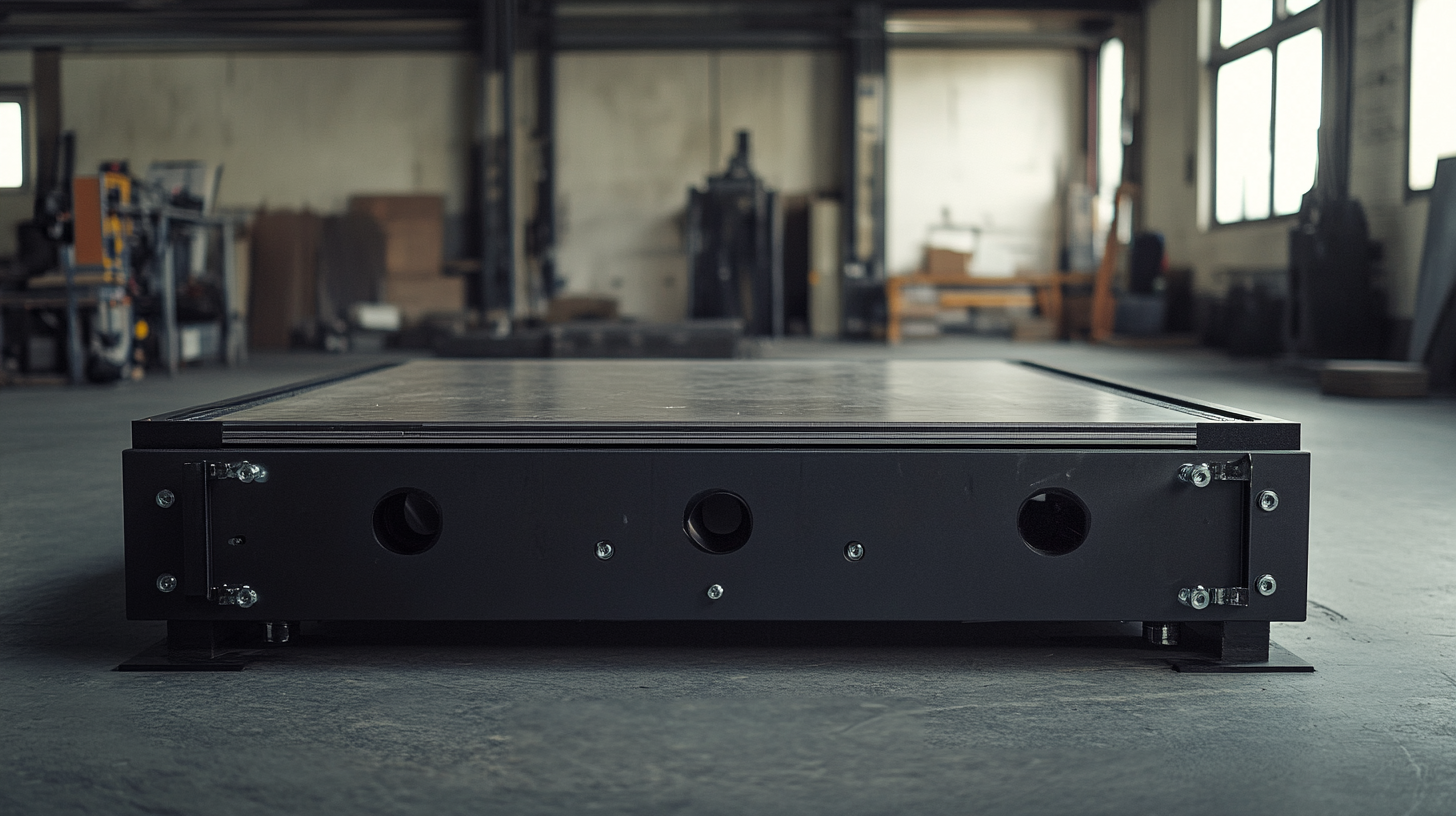
The Advantages of Using CNC Plasma Tables in Modern Fabrication
CNC plasma tables have revolutionized modern fabrication, offering numerous advantages that enhance precision and efficiency in metalworking processes. According to a report from MarketsandMarkets, the global CNC plasma cutting market is expected to grow significantly, with an estimated compound annual growth rate (CAGR) of 5.6% from 2021 to 2026. This growth is driven by the increasing demand for high-quality cutting technologies in industries such as automotive, aerospace, and construction.
One of the primary advantages of CNC plasma tables is their ability to produce high-quality cuts at remarkable speeds. Traditional cutting methods often struggle with maintaining accuracy over complex designs, but CNC plasma cutting systems can consistently achieve tolerances as tight as ±0.5 mm. This level of precision is crucial for industries requiring detailed and intricate patterns, helping manufacturers reduce waste and increase productivity. A study published by the Fabricators & Manufacturers Association International indicates that adopting CNC plasma technology can lead to a reduction in operational costs by up to 30% due to its speed and efficiency.
Furthermore, CNC plasma tables are incredibly versatile, allowing for the cutting of various materials including steel, aluminum, and stainless steel. The American Welding Society reports that plasma cutting technology has expanded its applications beyond traditional metalworking, now encompassing sectors such as art metalwork and signage. This versatility not only broadens the scope of projects that can be undertaken but also attracts a wider range of fabricators who seek innovative cutting solutions to cater to diverse customer needs. Embracing this technology not only optimizes production capabilities but also strengthens a company’s market position in an increasingly competitive landscape.
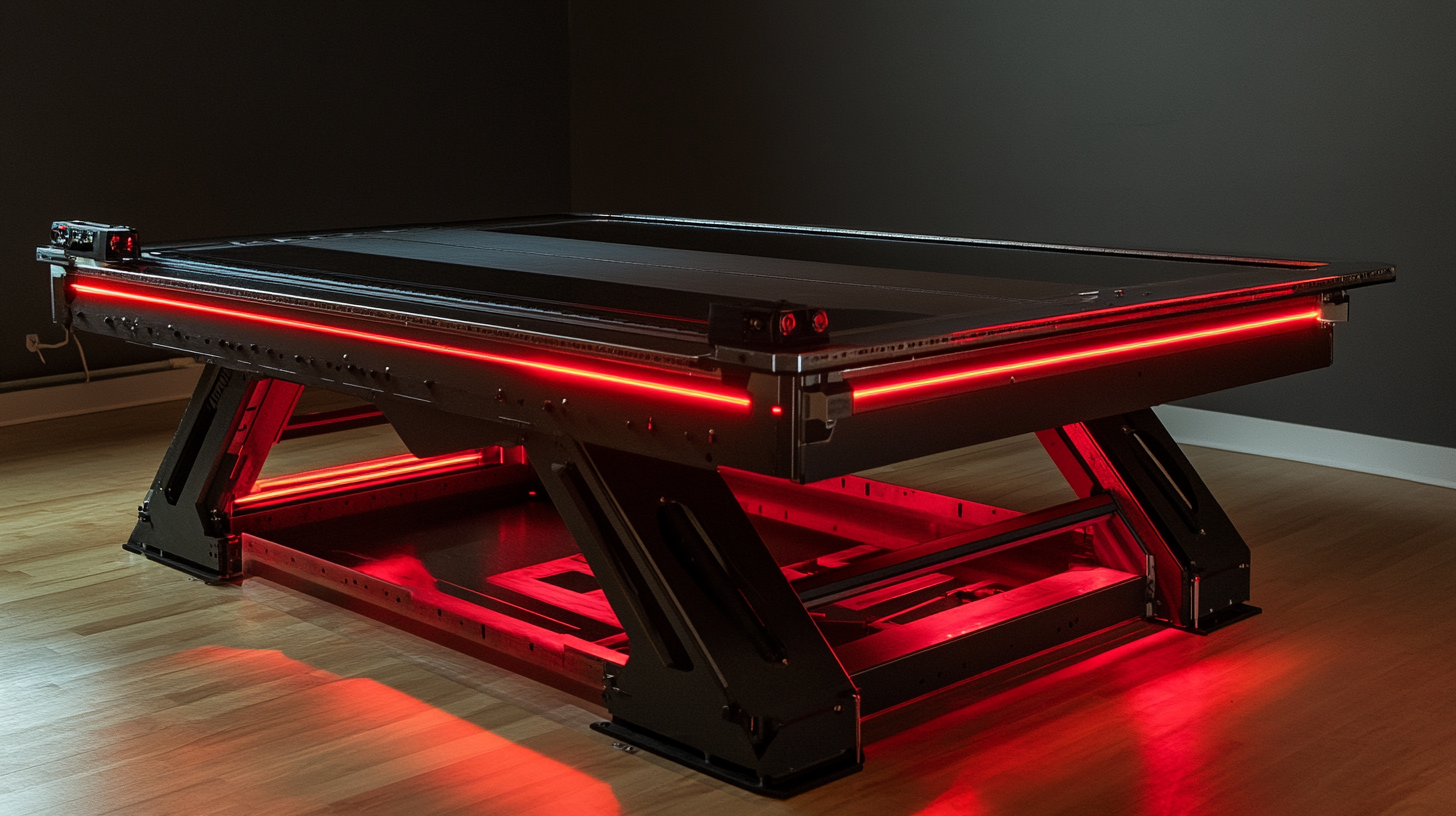
Factors to Consider When Choosing a CNC Plasma Table for Your Workshop
When selecting a CNC plasma table for your workshop, there are several critical factors to consider that can significantly impact your efficiency and production quality. First and foremost, the size of the table is essential. According to a report by the Fabricators & Manufacturers Association (FMA), the demand for larger CNC plasma tables has surged by over 25% in recent years, as businesses seek to accommodate larger workpieces and improve cutting flexibility. Understanding the typical dimensions of the materials you will be working with allows you to choose a table that meets your specific needs without unnecessary constraints.
Another factor to consider is the cutting speed and precision of the CNC plasma table. Industry benchmarks indicate that high-definition plasma systems can operate at speeds up to 300 inches per minute with an accuracy of ±0.005 inches. This precision is vital for projects requiring detailed cuts and intricate designs. Assessing the machine's specifications in relation to the materials you plan to work with will help ensure that you achieve high-quality results while also maximizing productivity.
Additionally, software compatibility and ease of use are crucial considerations. A study by the Association for Manufacturing Technology (AMT) highlighted that manufacturers are increasingly leveraging advanced CAD/CAM software integrated with CNC machines, which enhances overall workflow efficiency. Ensuring that the CNC plasma table you choose can easily interface with your existing software systems will streamline your operations and reduce the learning curve.
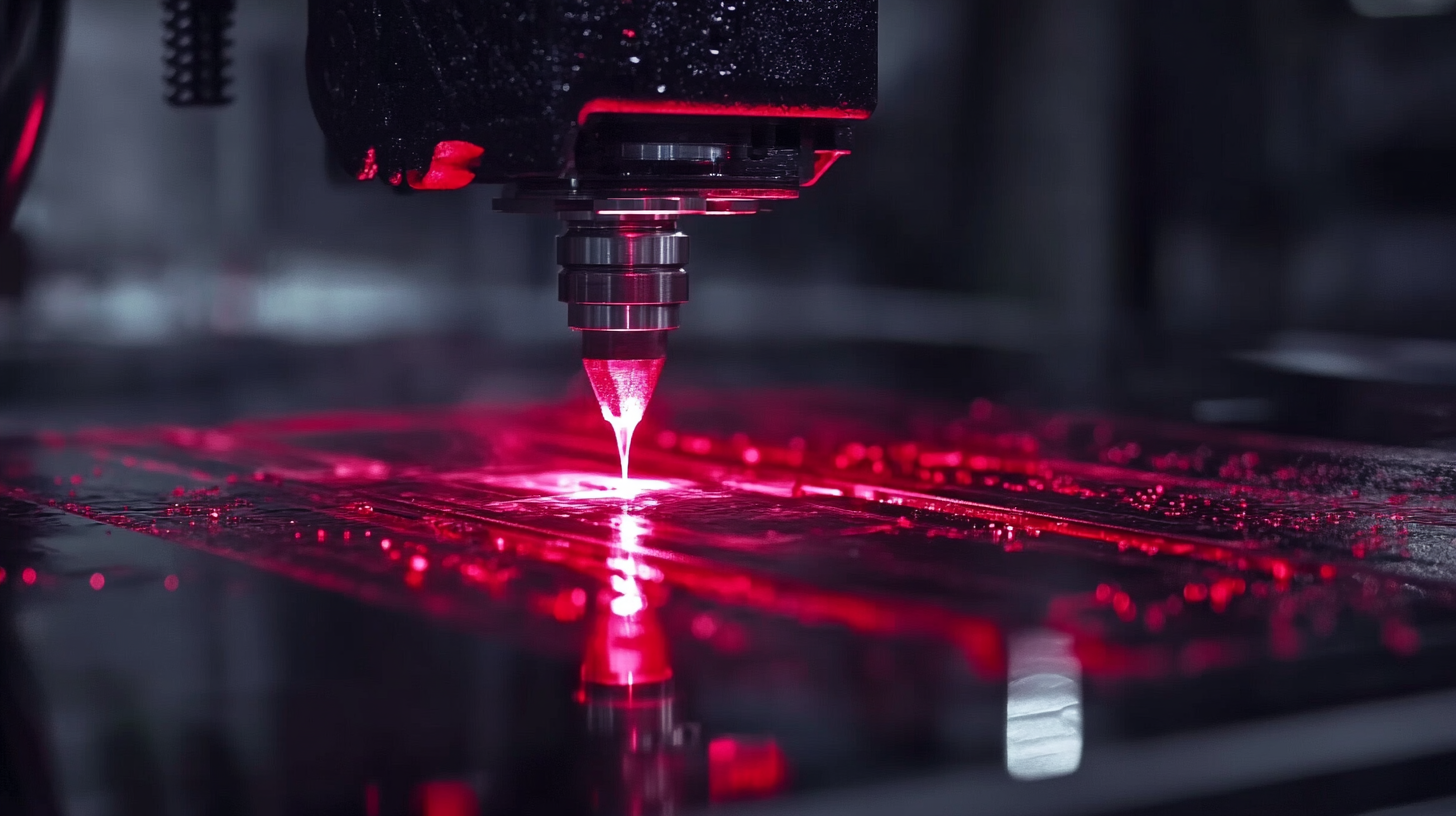
Comparing Different Types of CNC Plasma Tables: Which One is Right for You?
When selecting a CNC plasma table, understanding the different types available is essential to meeting your specific needs. CNC plasma tables can be broadly categorized into entry-level, mid-range, and high-end options, each offering varying degrees of precision, cutting speed, and software capabilities. Entry-level models are typically more affordable and suitable for hobbyists or small businesses, while mid-range options provide enhanced features like better cutting quality and more automated processes. High-end machines cater to industrial applications, featuring advanced nesting software that optimizes material use, thus minimizing waste.
According to industry reports, the precision of CNC plasma cutting can be affected by several factors, including the type of plasma torch used and the quality of the control system. For example, machines equipped with automatic nesting tools significantly reduce scrap material, maximizing efficiency. Reports indicate that proper nesting can lead to savings of up to 20% in raw material costs, making it a crucial feature for manufacturers focused on cost efficiency.
Additionally, when choosing a CNC plasma table, consider the available software compatibility. Many systems now come with intuitive CAD/CAM software that allows users to design their cuts digitally, adjusting parameters for different materials. This flexibility not only increases productivity but also ensures higher accuracy in the final cuts. With many options on the market, it's important to assess both immediate project needs and long-term operational goals to choose the right CNC plasma table for your setup.
Essential Maintenance Tips to Extend the Lifespan of Your CNC Plasma Table
Maintaining a CNC plasma table is crucial for ensuring its longevity and optimal performance. According to a report by the Fabricators & Manufacturers Association, effective maintenance can extend the lifespan of such machines by up to 50%. Routine care not only enhances productivity but also reduces downtime and repair costs, making it essential for businesses looking to maximize their investment.
Firstly, regular cleaning is fundamental to the maintenance process. Plasma tables accumulate residue from metal cutting, which can interfere with their operation and lead to premature wear. It is recommended to clean the table surface and components weekly, utilizing appropriate cleaning solutions that won’t corrode the metal parts. Furthermore, maintaining the integrity of the water table is vital; changing the water frequently prevents rust formation and helps cool down the operating machinery, which is critical during high-usage periods.
Additionally, inspecting and replacing consumables like plasma torch tips and electrodes can significantly improve cutting quality and efficiency. According to industry studies, worn-out consumables can lead to a 15% reduction in cutting speed and increased energy consumption. Operators should adhere to the manufacturer's guidelines for replacement intervals based on usage hours to ensure peak performance. Regularly checking for software updates and calibrating the machine can also enhance operational reliability, ensuring that your CNC plasma table remains a versatile tool for various projects.