Unlock Precision and Efficiency: Explore the Future with Plasma Laser Cutters for Modern Manufacturing
In the rapidly evolving landscape of modern manufacturing, precision and efficiency have become paramount for staying competitive. According to a report by MarketsandMarkets, the global laser cutting market is projected to grow from $4.5 billion in 2020 to $6.5 billion by 2025, with advanced technologies like Plasma Laser Cutters leading the charge. These innovative tools not only enhance cutting precision but also significantly reduce production times, making them indispensable for a wide range of industries including automotive, aerospace, and metal fabrication. As manufacturers increasingly pivot towards automation and smart technologies, plasma laser cutters are emerging as game-changers that redefine operational capabilities.
With the adoption of Plasma Laser Cutters, businesses can achieve intricately detailed cuts with various materials, thereby increasing their versatility in production. A report from ResearchAndMarkets indicates that the demand for such advanced cutting technologies is heavily driven by the rising need for lightweight components and complex geometries that traditional methods struggle to produce. This blog will explore how plasma laser cutting technology is transforming manufacturing processes, offering insights into its benefits, applications, and potential for future advancements. Join us as we delve into the pivotal role of Plasma Laser Cutters in shaping the future of precision manufacturing.
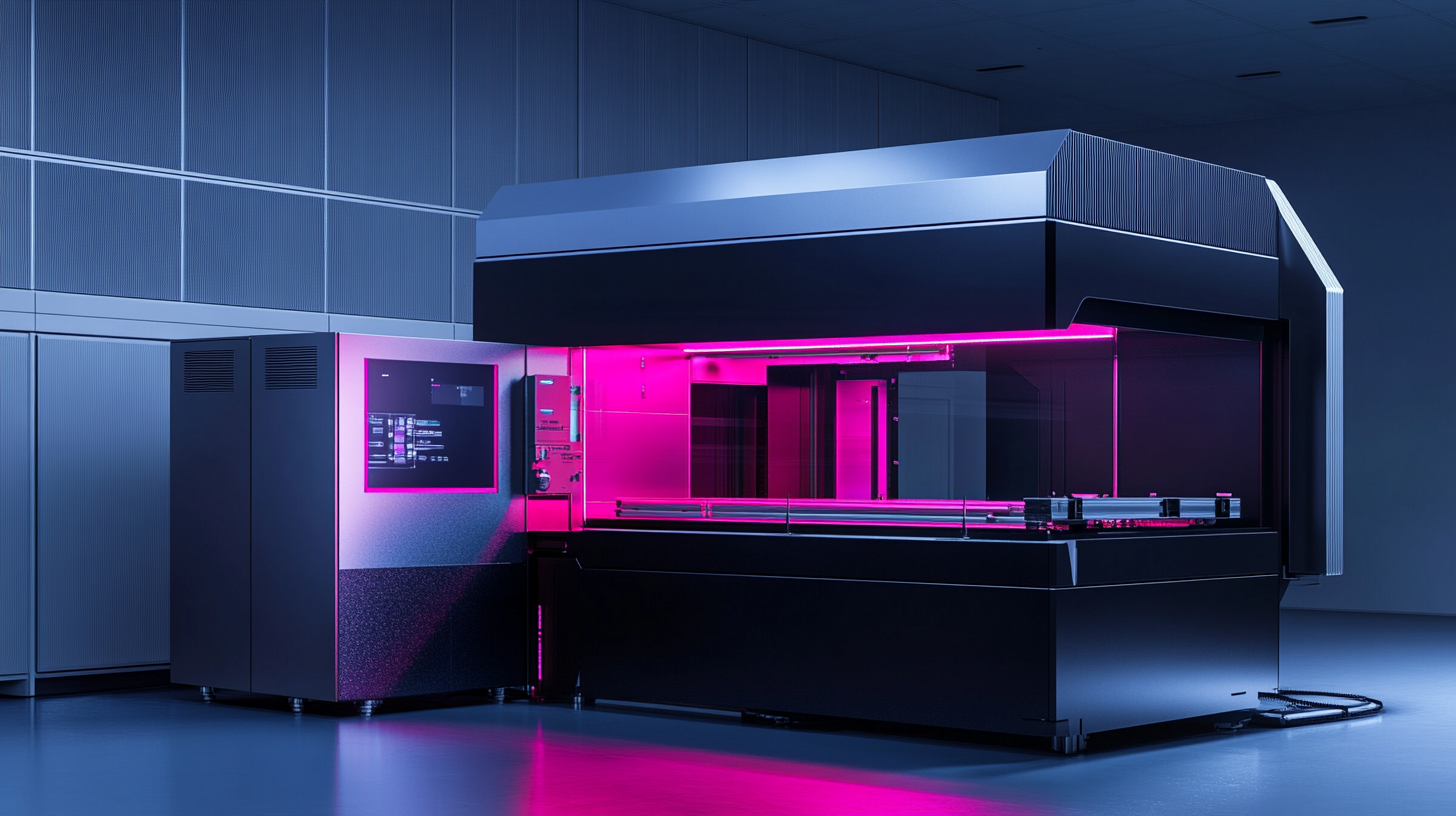
Revolutionizing Manufacturing: The Rise of Plasma Laser Cutting Technology
The manufacturing landscape is witnessing a transformative shift with the emergence of plasma laser cutting technology. This revolutionary approach melds the precision of traditional laser cutting with the speed and efficiency of plasma cutting, creating a powerful tool for modern manufacturers. By harnessing high-energy plasma and laser beams, this technology can effortlessly slice through various materials with remarkable accuracy, drastically reducing production times while ensuring a clean finish. As industries lean towards automation and digital manufacturing, plasma laser cutters offer an enticing solution. Their ability to operate at high speeds without compromising on quality makes them ideal for a range of applications, from automotive to aerospace. Furthermore, the flexibility of this technology accommodates diverse materials, including metals, plastics, and composites, allowing businesses to adapt quickly to evolving market demands. The rise of plasma laser cutting technology is not just a matter of speed; it also emphasizes efficiency. By minimizing material waste and energy consumption during the cutting process, manufacturers can significantly reduce operational costs. This sustainability component aligns with the growing emphasis on eco-friendly practices within the industry. As businesses seek to optimize their production processes, embracing this cutting-edge technology will likely become a standard rather than an option, leading the way to a new era of manufacturing excellence.
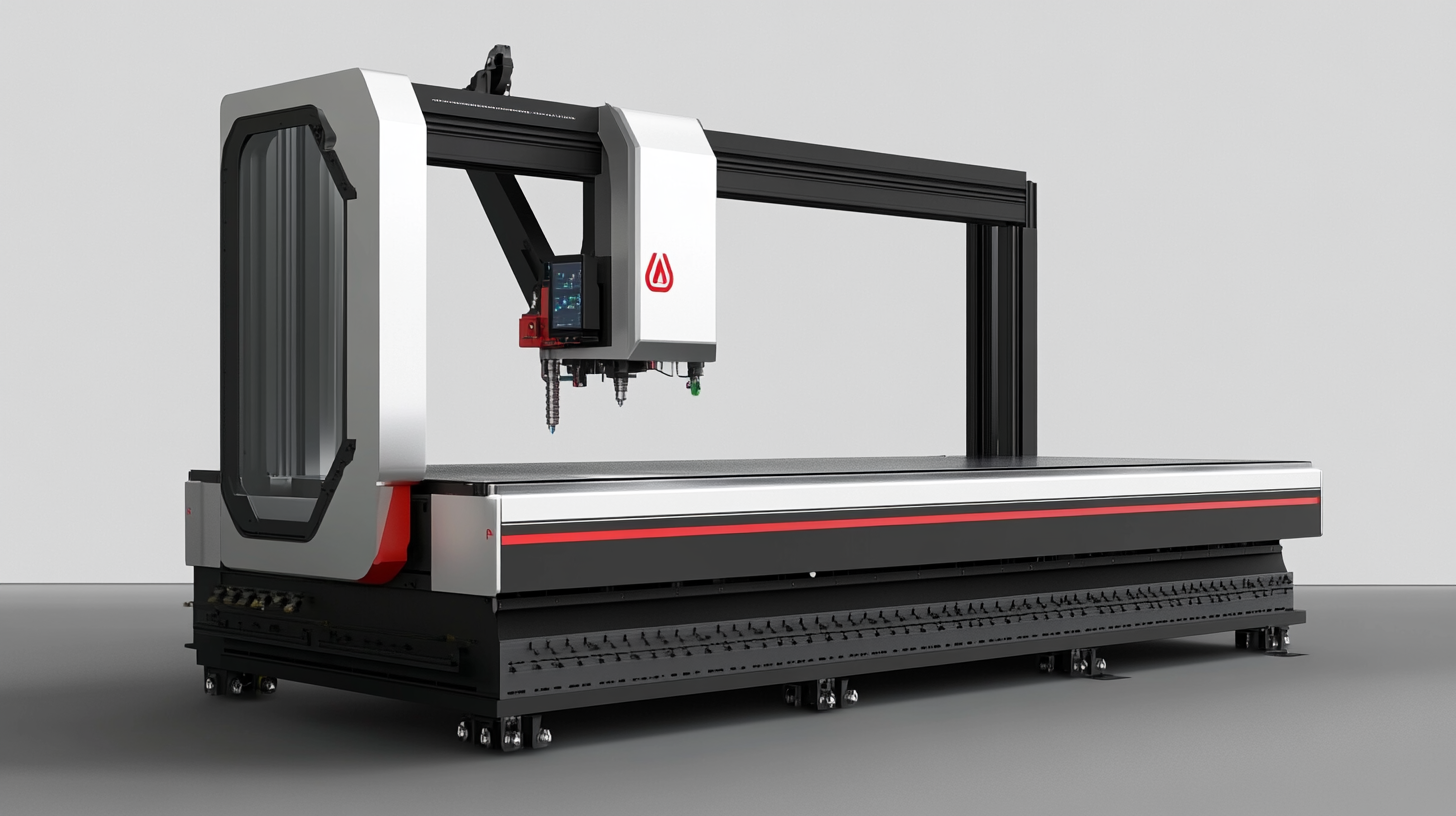
Precision Engineering: How Plasma Laser Cutters Achieve Micron-Level Accuracy
In the realm of modern manufacturing, precision is paramount. Plasma laser cutters have emerged as a groundbreaking technology that combines the best of both worlds—a laser's precision and plasma's speed—allowing manufacturers to achieve micron-level accuracy in their cutting processes. This innovative equipment utilizes high-energy plasma beams to cut through various materials with minimal waste and maximum efficiency, resulting in cleaner edges and finer details.
The ability of plasma laser cutters to operate at such fine tolerances unlocks new opportunities for industries ranging from aerospace to automotive. By employing advanced control systems and real-time feedback mechanisms, these machines ensure that every cut is executed with unparalleled precision. Manufacturers can now create complex geometries and intricate designs that were once thought impossible, opening up a new frontier in product development and customization.
Furthermore, the versatility of plasma laser technology allows it to work seamlessly with a variety of materials, including metals, plastics, and composites. This adaptability, when paired with the micron-level accuracy, positions plasma laser cutters as essential in enhancing productivity while maintaining high-quality standards. As manufacturers continue to pursue greater efficiency and innovation, plasma laser cutters stand out as a key asset in achieving these goals.
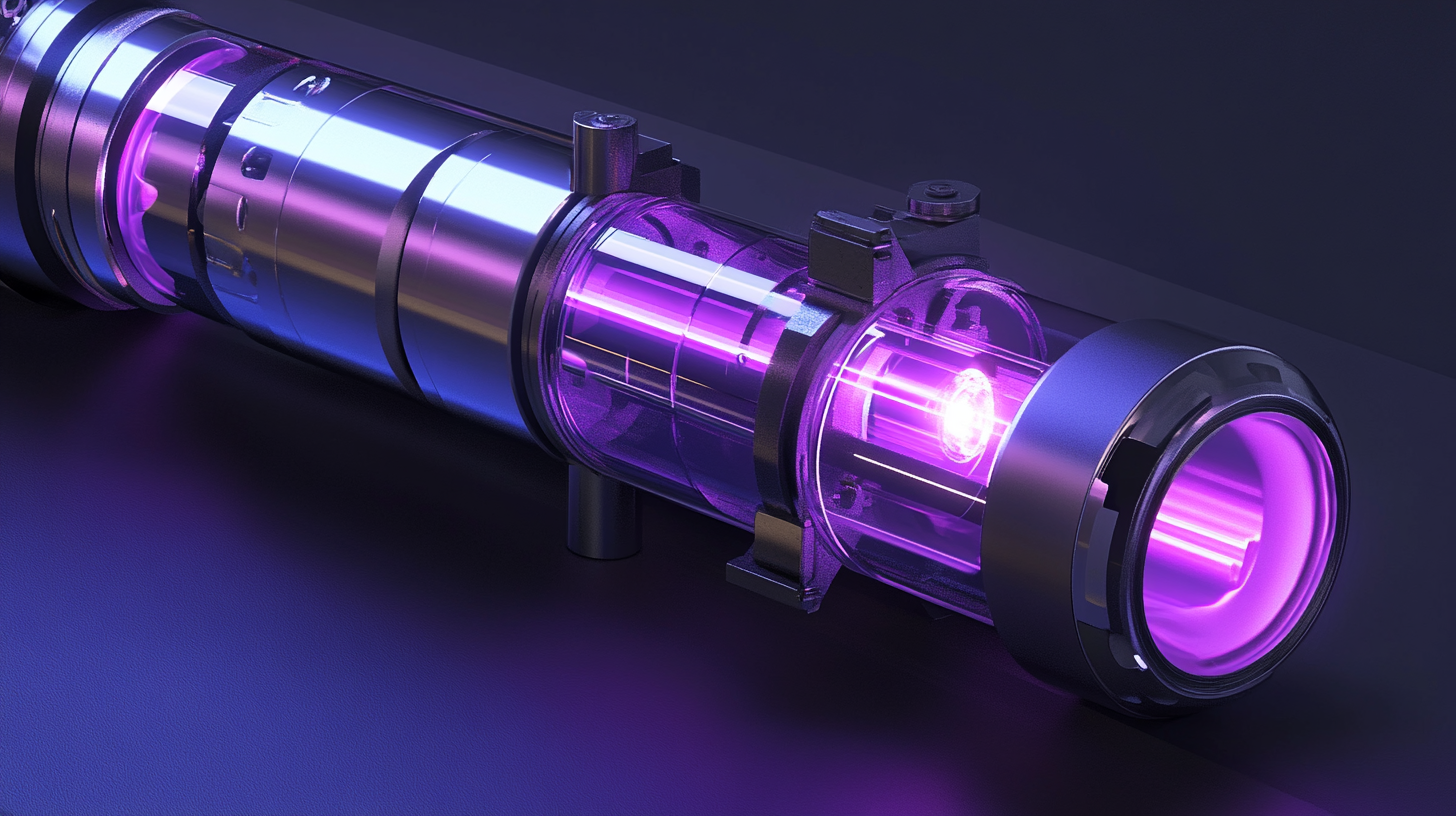
Efficiency Metrics: Reducing Production Time and Material Waste with Plasma Lasers
In the rapidly evolving landscape of modern manufacturing, plasma laser cutters have emerged as a game-changer, redefining the benchmarks for efficiency. By harnessing the power of high-precision cutting, these advanced tools significantly reduce production time, allowing manufacturers to meet tight deadlines without sacrificing quality. The high-speed processing capabilities of plasma lasers facilitate seamless operations, enabling manufacturers to streamline workflows and enhance overall productivity.
One of the standout benefits of utilizing plasma laser technology is the substantial decrease in material waste. Traditional cutting methods often lead to significant off-cuts and inefficiencies, whereas plasma lasers provide a cleaner cut with minimal kerf. This precision not only saves materials but also reduces costs associated with purchasing raw materials, translating into considerable savings for businesses. By optimizing material usage, manufacturers can adopt a more sustainable approach, aligning with the increasing demand for eco-friendly practices in industry.
Furthermore, efficiency metrics associated with plasma laser cutters extend beyond just speed and waste reduction. The adaptability of these machines allows for precise adjustments tailored to different materials and thicknesses, broadening their application spectrum. This versatility means that manufacturers can cater to diverse project requirements without needing extensive retooling, further enhancing operational efficiency. As plasma laser technology continues to advance, it is poised to play a pivotal role in shaping the future of manufacturing, driving both innovation and sustainability.
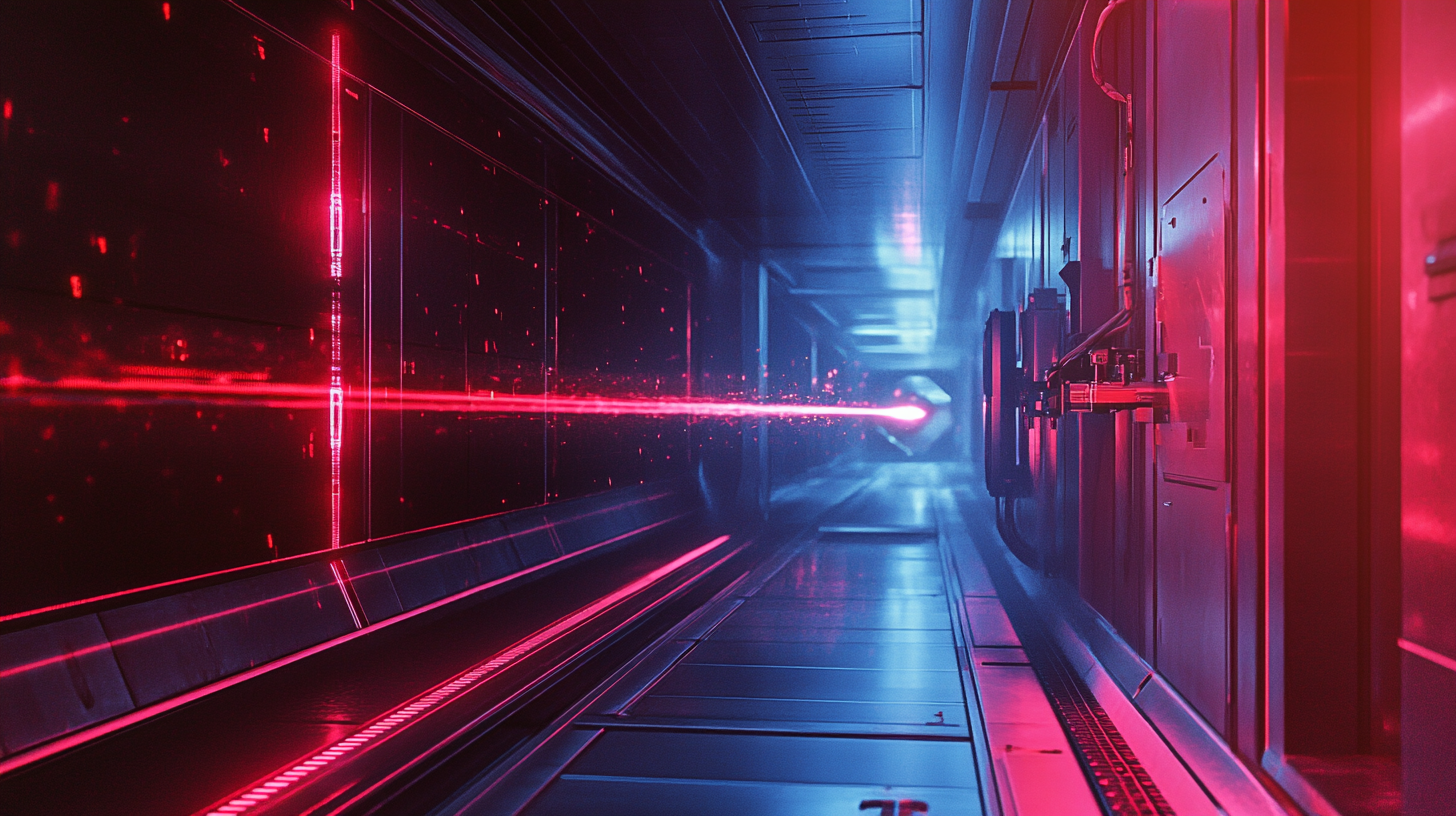
Cost-Effectiveness: Analyzing Operational Savings from Plasma Laser Cutter Adoption
The manufacturing landscape is rapidly evolving, with the integration of advanced technologies driving significant operational changes. Among these innovations, plasma laser cutters stand out not only for their precision but also for their cost-effectiveness. Adopting plasma laser cutting technology allows manufacturers to streamline their processes, resulting in substantial savings over time.
One of the primary operational advantages of plasma laser cutters is their efficiency in handling diverse materials, from metals to plastics. Traditional cutting methods often require multiple setups and configurations, increasing labor costs and project timelines. In contrast, plasma laser cutters can adapt to various materials and thicknesses with minimal adjustments, reducing downtime and optimizing workflow. This versatility helps manufacturers save on both labor and operational costs, enabling them to redirect resources to other critical areas.
Moreover, the speed at which plasma laser cutters operate significantly lowers operational expenditures. With high cutting speeds and reduced material waste, companies can achieve faster turnaround times and higher output levels. The combination of enhanced productivity and reduced scrap not only improves profit margins but also enhances competitiveness in a crowded market. As businesses increasingly seek solutions that deliver both quality and efficiency, the case for investing in plasma laser cutters as a means of cutting costs becomes increasingly compelling.
Future Trends: Innovations in Plasma Laser Technology and their Impact on Manufacturing Industries
The rapid advancements in plasma laser technology are reshaping manufacturing methodologies and driving unprecedented efficiency. A recent report highlighted that the laser and additive manufacturing industry in Guangdong aims to achieve a double industrial scale growth from 900 billion to 1,800 billion RMB by 2025, emphasizing the critical role that innovative plasma laser technologies play in this growth trajectory. As industries continue to adopt these cutting-edge tools, they unlock greater precision and enable the fabrication of increasingly complex components.
Moreover, the latest insights from the 2024 China Laser Industry Development Report suggest that the integration of plasma laser systems into production processes not only enhances operational productivity but also contributes significantly to cost savings. As manufacturers grapple with competitive pressures, investing in plasma laser cutters represents a strategic move towards sustaining a leadership position in the rapidly evolving market. The technology promises to streamline processes while ensuring quality, reflecting a shift towards more sustainable and efficient manufacturing practices.
Recent events such as the 21st Fiber Optic Communication Market and Technology Symposium highlight the industry's commitment to innovation amidst a backdrop of fierce competition. The laser technology landscape is becoming a cornerstone for the future of manufacturing, as evidenced by the recurring themes of high-quality development and technological breakthroughs showcased at these gatherings. As manufacturers embrace these innovations, they stand poised to redefine their operational capacities and accelerate their journey toward enhanced industrial excellence.