Unlocking Precision and Efficiency with Custom Plasma Cutting Solutions
The manufacturing industry is at the forefront of technological advancement, with precision and efficiency becoming paramount in maintaining competitive advantage. According to a recent industry report by Grand View Research, the global plasma cutting equipment market is projected to reach USD 7.12 billion by 2025, with a compound annual growth rate (CAGR) of 5.7% from 2019 to 2025. This growth underscores the increasing demand for advanced cutting solutions that not only enhance productivity but also minimize material waste. Among these solutions, Custom Plasma Cutting has emerged as a key player, offering tailored specifications that meet the unique requirements of various industrial applications.
Custom Plasma Cutting technology enables manufacturers to achieve intricate designs and precision cuts that standard methods may struggle to deliver. Research from the Fabricators & Manufacturers Association indicates that companies utilizing custom plasma cutting solutions report up to a 30% reduction in production time and a significant decrease in operational costs. By investing in custom solutions, businesses can optimize their workflows, enhance the quality of their products, and respond more effectively to the dynamic demands of the market. As industries continue to evolve, the significance of Custom Plasma Cutting cannot be overstated; it is not just a tool, but a crucial driver for innovation and efficiency in production.
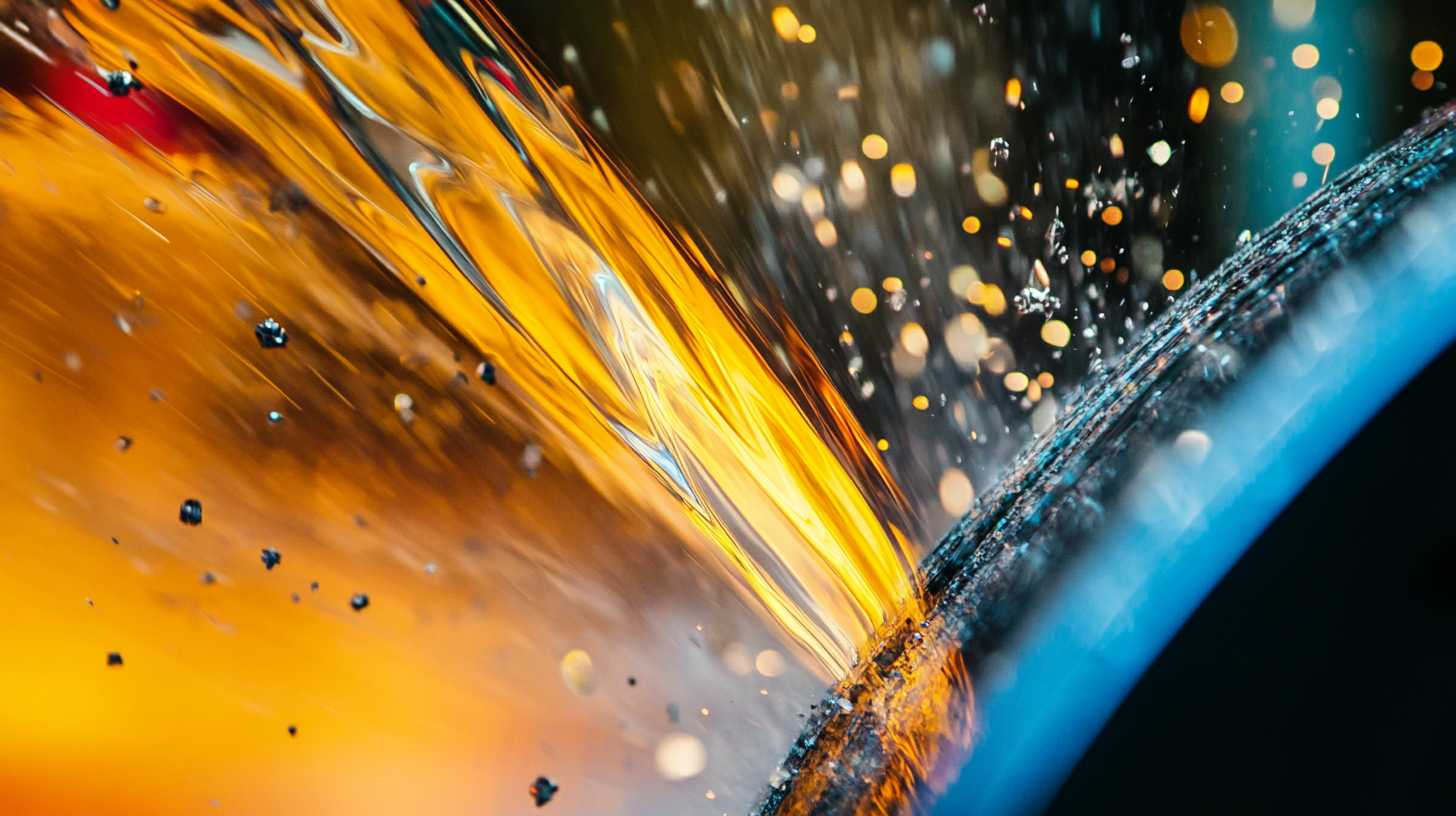
The Advantages of Custom Plasma Cutting Solutions in Modern Manufacturing
In the fast-paced world of modern manufacturing, the demand for precision and efficiency has never been greater. Custom plasma cutting solutions have emerged as a critical technology that enhances production effectiveness across various industries. According to a report by Technavio, the global plasma cutting equipment market is projected to grow by 5.6% annually, reflecting the increasing adoption of advanced cutting methods in manufacturing. This growth underscores the importance of tailored solutions to meet specific operational needs, ultimately resulting in higher quality outputs and reduced wastage. One of the key advantages of custom plasma cutting solutions is their ability to deliver high levels of precision. Standard cutting methods often fall short in meeting the exact specifications required by complex projects. A study by Research and Markets indicates that precision cutting can improve the overall efficiency of workflows by up to 30%, significantly enhancing productivity. Customization allows manufacturers to program machines to perform intricate cuts, reducing the need for secondary processes and enabling faster turnaround times. Moreover, tailor-made plasma cutting systems can optimize material usage, a vital consideration in today’s sustainability-focused manufacturing landscape. By minimizing scrap and maximizing yield, custom solutions not only lead to cost savings but also align with environmental goals. Industry data from the Fabricators & Manufacturers Association (FMA) indicates that efficiency improvements in cutting processes can reduce material waste by as much as 15%. This synergy between customization and efficiency positions businesses to not only thrive economically but also contribute positively to environmental stewardship.
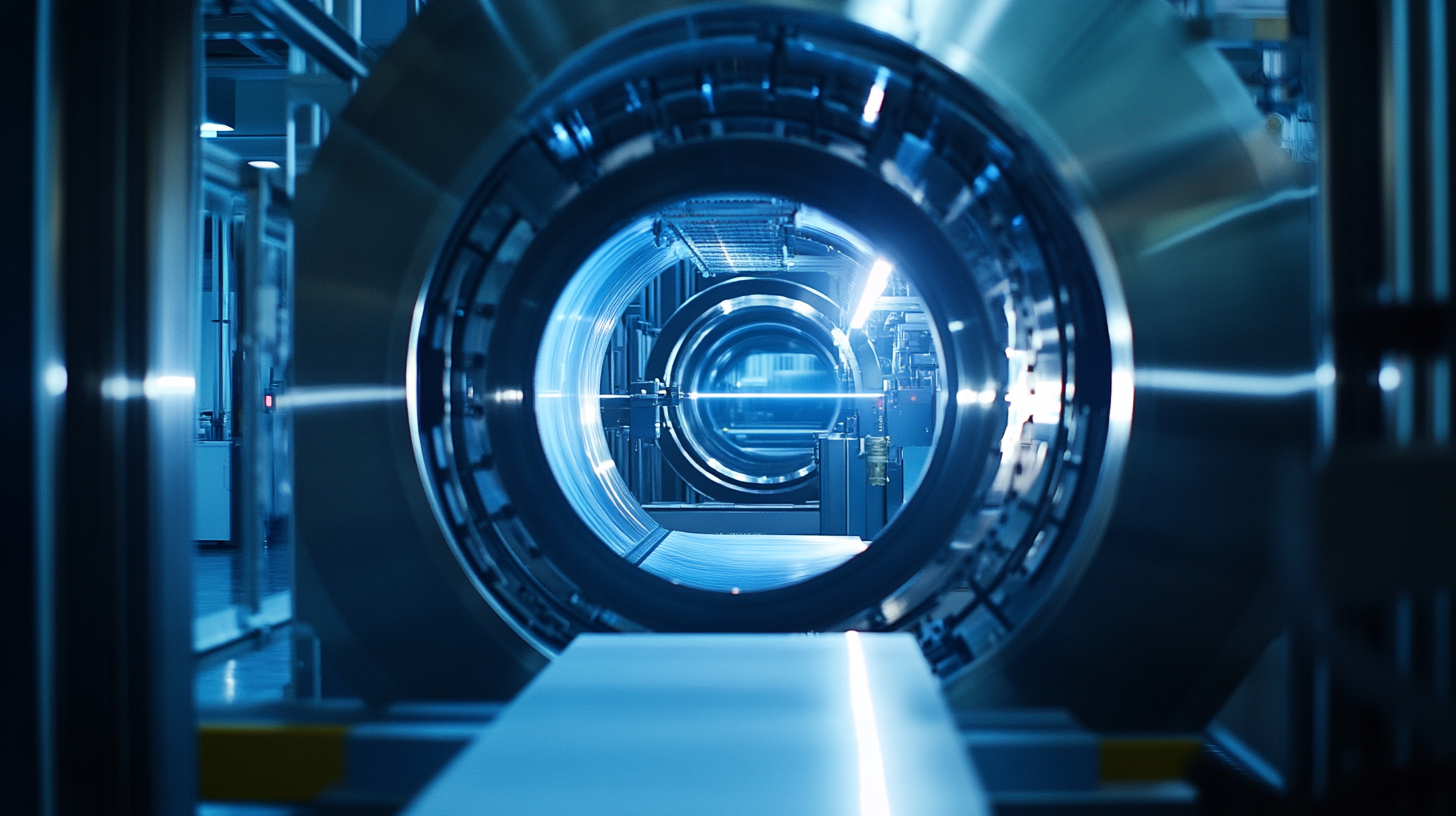
How Custom Plasma Cutting Enhances Precision in Metal Fabrication
Custom plasma cutting solutions have revolutionized the metal fabrication industry by enhancing precision and efficiency in various applications. Traditional cutting methods often struggle with intricate designs and tight tolerances, whereas custom plasma cutting systems are specifically designed to meet the unique needs of each project. With advanced technology, these systems utilize a high-temperature plasma arc to melt and swiftly cut through metals, resulting in clean and accurate edges that traditional methods simply cannot achieve.
One of the main benefits of custom plasma cutting is its adaptability. Manufacturers can tailor the cutting parameters such as speed, pressure, and power levels to suit the specific material and thickness being processed. This level of customization ensures that each cut is not only precise but also optimized for efficiency, thereby reducing waste and saving valuable time in production. Additionally, the ability to create complex shapes and designs with high fidelity makes plasma cutting an invaluable tool for industries ranging from automotive to aerospace.
Moreover, the integration of computer numerical control (CNC) technology with plasma cutting systems further enhances precision. CNC plasma cutters can replicate intricate designs with remarkable accuracy, allowing for high-volume production without compromising on quality. This technology minimizes the risk of human error, ensuring that each piece produced meets stringent specifications. As a result, businesses are able to deliver superior products that satisfy the increasing demands for higher quality and performance in metal fabrication.
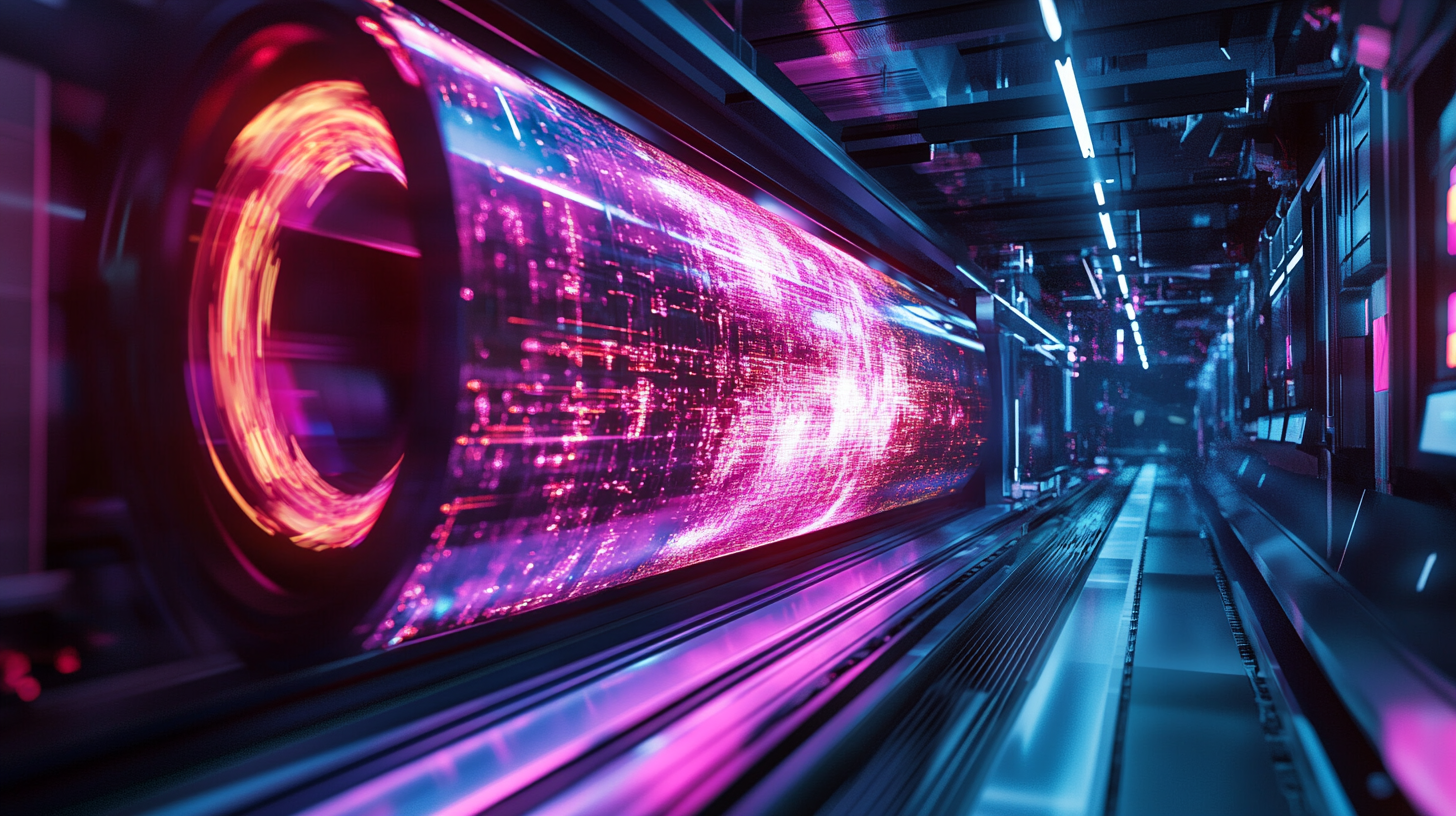
Exploring the Efficiency Boost from Tailored Plasma Cutting Technologies
In today's fast-paced manufacturing landscape, efficiency is paramount. Custom plasma cutting solutions are revolutionizing how industries approach metal fabrication, offering significant boosts in productivity and accuracy. By integrating tailored plasma cutting technologies, companies can achieve results that not only meet but exceed their specific operational needs. This level of customization allows for a sharper focus on material thickness, type, and intricate design specifications, ensuring that each cut is executed perfectly.
The potential for enhanced efficiency begins with the precision of the cutting process. Custom plasma systems can be programmed to adapt to various materials and contours, minimizing wasted time and resources associated with trial and error. As a result, manufacturers experience shorter production cycles and reduced downtime. Furthermore, the advanced capabilities of bespoke plasma cutting setups eliminate the need for extensive post-processing, aligning perfectly with just-in-time production systems that many companies are striving to adopt.
Moreover, these tailored solutions often come equipped with cutting-edge technologies such as automated nesting and real-time data analysis. This integration of smart technology not only streamlines operations but also empowers businesses to make data-driven decisions, optimizing overall workflow. As industries continue to evolve, the emphasis on customized plasma cutting systems signifies a forward-thinking approach to embracing efficiency, ultimately reshaping the future of metal fabrication.
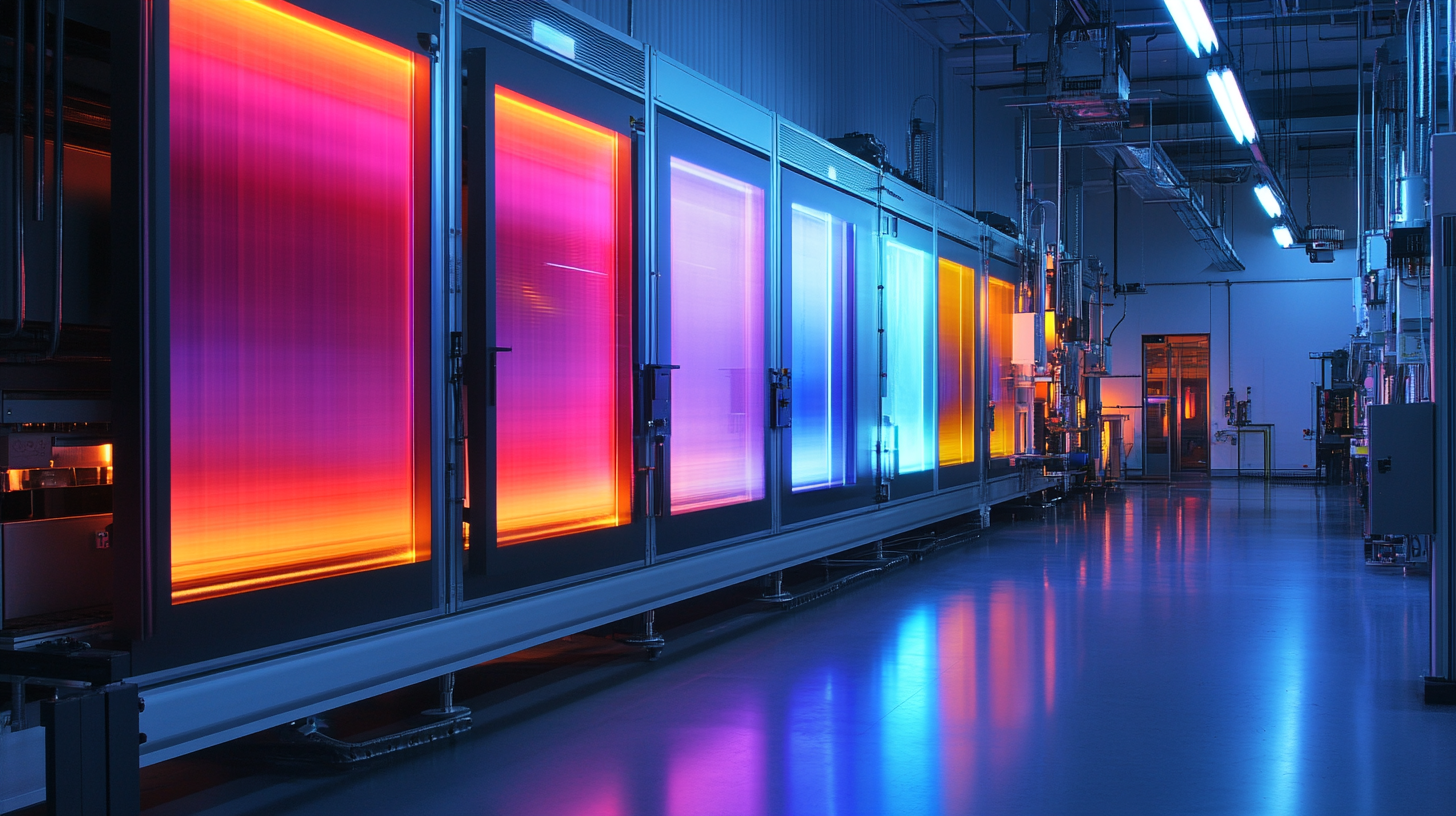
Key Industries Benefiting from Advanced Custom Plasma Cutting Solutions
The adoption of advanced custom plasma cutting solutions has significantly transformed key industries, enhancing precision and efficiency in various applications. In recent developments, the CNC plasma cutting machines market is projected to witness notable growth, with an estimated market value of USD 673.2 million in 2024. Analysts forecast a compound annual growth rate (CAGR) of over 5.1% from 2025 to 2034, highlighting the rising demand for automated and highly customizable cutting solutions.
Industries such as manufacturing, aerospace, and automotive are particularly benefitting from these innovations. Robotic plasma cutting systems, as illustrated by recent advancements in 3D robotic plasma cutting technologies, are enabling seamless integration into production lines, thus improving operational workflows. These systems leverage essential offline programming tools, streamlining processes and reducing material waste.
Additionally, the welding and cutting equipment market is on the rise, with a projected expansion rate corroborated by industry reports predicting a significant year-on-year growth trajectory. Regions like Saudi Arabia, UAE, and Qatar are anticipated to contribute to this growth, underlining the importance of plasma cutting technology in sectors such as construction and energy. This evolving landscape clearly indicates the critical role of custom plasma cutting solutions in meeting the evolving needs of modern industries.
Future Trends in Custom Plasma Cutting: Innovation and Sustainability
The landscape of custom plasma cutting is rapidly evolving, driven by innovation and sustainability. Industry reports indicate that the global plasma cutting market is projected to grow significantly, with an estimated CAGR of 6.5% from 2023 to 2030. This growth is primarily fueled by advancements in technology, which are improving precision and efficiency in cutting processes. Modern plasma cutting systems are now equipped with real-time monitoring and AI-driven diagnostics, ensuring not only enhanced accuracy but also the reduction of material waste.
Sustainability is becoming a key focus in the manufacturing sector, and plasma cutting is no exception. According to a report from Research and Markets, companies are increasingly adopting environmentally friendly practices, minimizing energy consumption during cutting operations. Innovative plasma systems now utilize hypertherm technology, which reportedly reduces operational costs by up to 30% while maintaining high-quality cuts. Furthermore, stringent regulations regarding emissions are pushing manufacturers to seek plasma cutting solutions that comply with green standards without compromising performance.
As the industry shifts towards sustainability, recyclable materials and reduced energy footprints are becoming standard metrics for success in custom plasma cutting projects. Manufacturers are exploring the potential of integrating renewable energy sources into their operations, further aligning with global sustainability goals. This transition not only enhances the reputation of companies within the pipeline but also attracts environmentally conscious clients looking for partners in innovation and responsibility. The future of custom plasma cutting is set to blend cutting-edge technology with a strong commitment to sustainability, paving the way for more responsible and efficient manufacturing practices.