When you work in metal fabrication, whether for business or pleasure, whether crafting tiny parts or large pieces, precision is vitally important. Even in metal fabrication artwork, while precision may not mean that something works properly, a precise cut will make all the difference in the aesthetic appeal of your artwork. Precision is important for a variety of reasons but when fabricating metal there are numerous obstacles to achieving ideal precision. Whether cutting carbon steel, aluminum steel, or aluminum, a CNC plasma cutting machine is the fastest way to do so while also achieving optimal accuracy and precision. Plasma cutting has been around for decades and the precision and accuracy only continues to improve over time.
Increased precision and accuracy are achieved through a variety of different options that are now available with CNC plasma cutting systems. Torches can be handheld but for better precision automated torch height control is beneficial. Additionally, there are a variety of different kinds and sizes of tables such as water tables, downdraft tables, and hybrid water/downdraft tables, each with their own unique advantages and disadvantages. TheFabricator.com explains how far plasma cutting technology has come and how maximum precision is achieved, “Today fabricators benefit from the combination of the innovations that emerged in the previous decades. The refinement of high-precision plasma technology, such as the HyDefinition® torches from Hypertherm and the FineLine® torches from InnerLogic Inc.; the advancement of electronic torch height control systems; and the evolution of computer control technology have resulted in a popular contour cutting solution.Machine motion has improved because of advancements made in linear guiding, servomotors, and gearing… Plasma cutting systems that feature these technologies have machine motion positioning accuracy of 0.004 inch. Systems of the past without sinusoidal AC servomotors, antibacklash gear heads, and precision linear guides normally would achieve only 0.015-in. positioning accuracy. The tighter tolerance as related to positioning accuracy minimizes corner overshoot and maintains straighter lines during diagonal moves. This higher accuracy in machine motion directly corresponds to higher part accuracy. The improvements to contouring technology, electronic torch height control, and high-precision torch systems enabled plasma machines to produce parts similar to laser-cut parts, but with slightly less accuracy. For example, 10-gauge cold-rolled steel sheet that’s laser-cut normally yields a part with an accuracy of ±0.005 in., while the same material cut with a high-precision plasma torch yields a part within ±0.012 in. Having said that, plasma cutting systems can cut thicker materials faster than lasers and produce quality parts at the same time.” When plasma cutting began the flame was achieved by using a jet of compressed air, also known as inert gas, a high voltage charge is applied to the jet which ionizes the gas and once heated to the ideal high temperature becomes plasma. The original plasma stream was larger and less precise but with advancements in technology the stream has become much more precise so that the best cuts can be achieved. This more accurate plasma stream, coupled with other technological advancements allows metal fabricators to make the kind of cuts that are comparable to laser cuts right in their own shops. When wanting to achieve a great deal of accuracy and precision for any kind of metal fabrication, choose from the wide variety of plasma cutting systems that are available in our shop at Machitech Automation.
CNC Plasma Cutting Achieves Optimal Precision
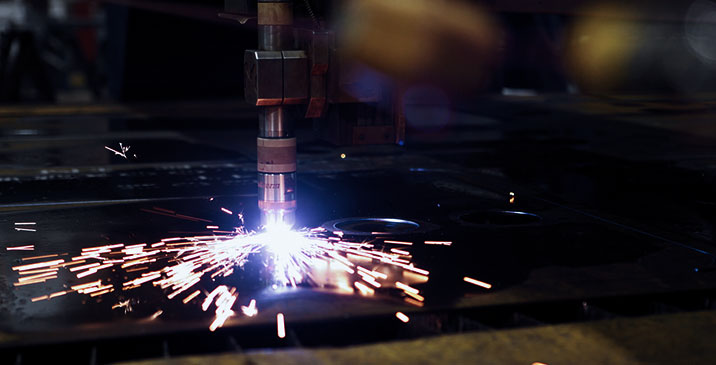